Internal combustion engines convert the chemical energy stored in fuel into the mechanical energy used to power machines when the fuel air mixture is compressed in the space between the piston and the cylinder head and ignited by the spark plug.
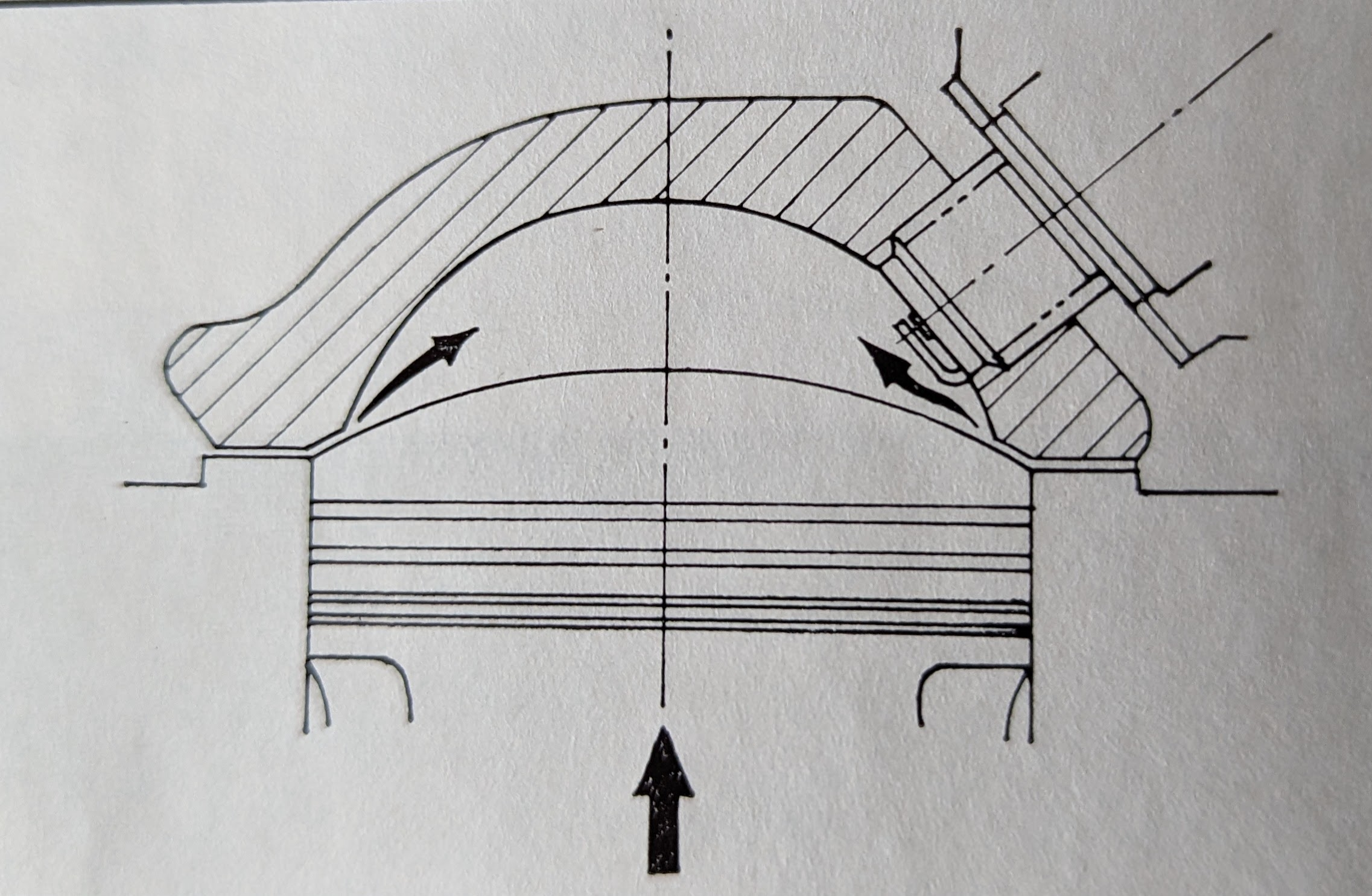
The design of the piston, cylinder and cylinder head plays an important role in determining the operating temperature of the engine. Finding ways to effectively dissipate heat has been a consistent challenge for makers of internal combustion engines since their invention, and the consequences of overheating can be serious, including piston seizures due to oil lubrication failure and damage to engine components caused by an issue called engine knock.
Engine Knock
As explained by Kevin Cameron, the technical expert at Cycle World, normal combustion is a controlled process that occurs when fuel and air are mixed in the correct proportions and ignited by a spark. The resulting flame front propagates through the mixture at a steady rate, producing a progressive release of energy to propel the piston downwards, driving the crankshaft. Knock (or "detonation"), on the other hand, occurs when some part of the unburned fuel becomes overheated and ignites spontaneously before the mixture has fully combusted, creating a shockwave. It is this uncontrolled, rapid explosion that gives the phenomenon its common name, knocking (or pinking/pinging), so called because of the distinctive noise the engine makes when this happens. The violent force caused by knocking can damage engine parts[1].
One way Honda and other manufacturers of air-cooled engines maintained operating temperatures at a level that minimised the chance of detonation was by using aluminium alloys - metals which have better heat conducting properties than iron and therefore dissipate heat more rapidly - in the construction of their engines[2].
Iron skull cylinder heads
The cylinder heads used in the early Super Cubs were made entirely of iron but these were superseded by heads constructed using aluminium alloy.
Although Honda eventually adopted all-aluminium heads, the C90s of the 60s and 70s came with a bimetallic head: the combustion chamber is made from iron and the remainder of the head is created with aluminium that has been cast around this iron "skull".
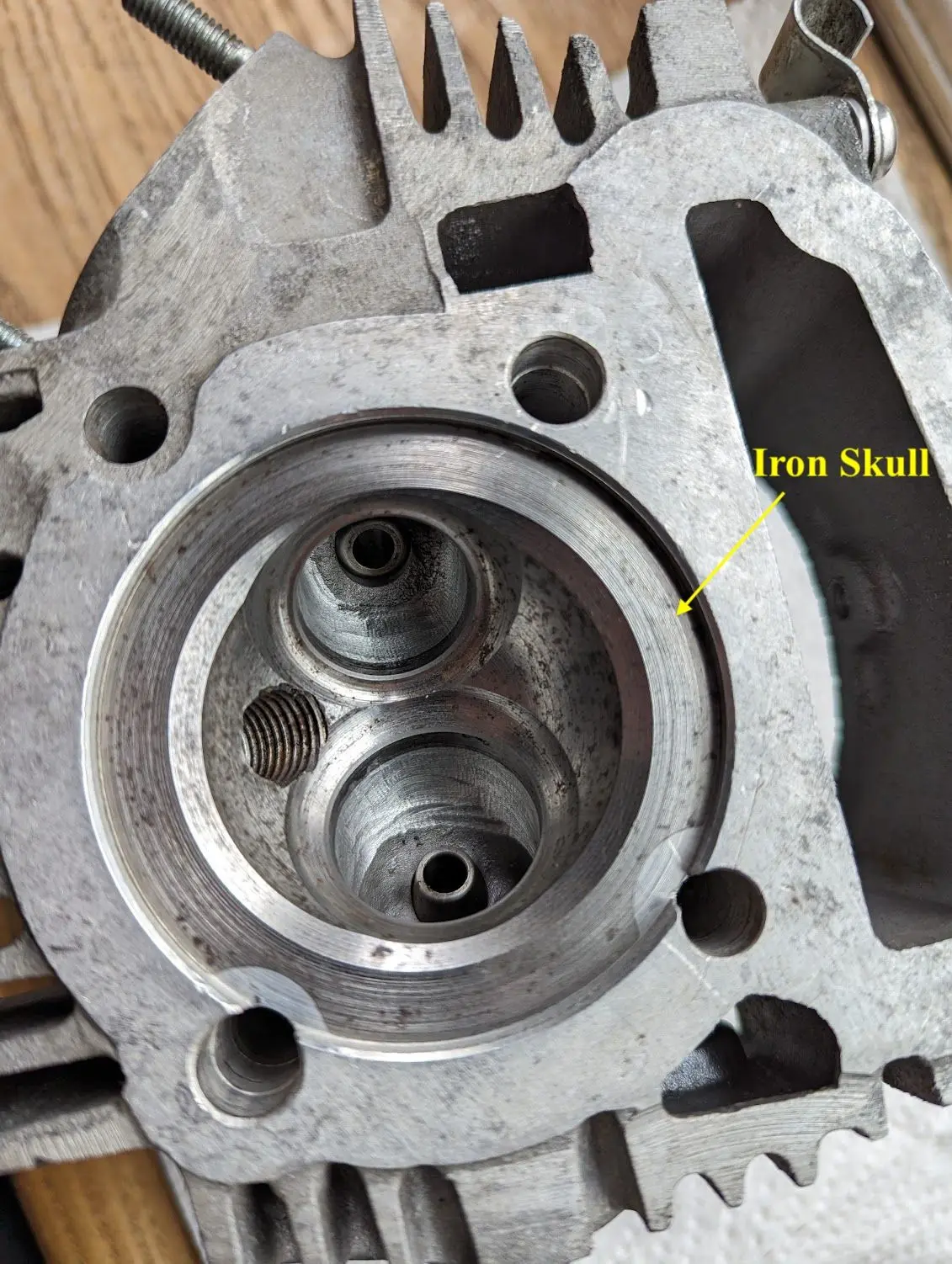
The continued use of iron in the cylinder head will presumably have resulted in relatively higher engine temperatures, so it is not obvious why Honda chose to do this. A clue might be that the same type of head was used on many of the Honda twins of the same era and other manufacturers, including Laverda and Susuki, did the same, perhaps indicates there were challenges manufacturing all-aluminium heads at this time[3].
It seems that, whatever the difficulties were, they had been overcome by the mid 70s and Honda motorcycles started to be fitted with all-aluminium heads from this point. The 1974 CT90 model - which otherwise shared the same engine as the C90 - got an all-aluminium head, although this was not fitted to the 6v C90s in the UK.
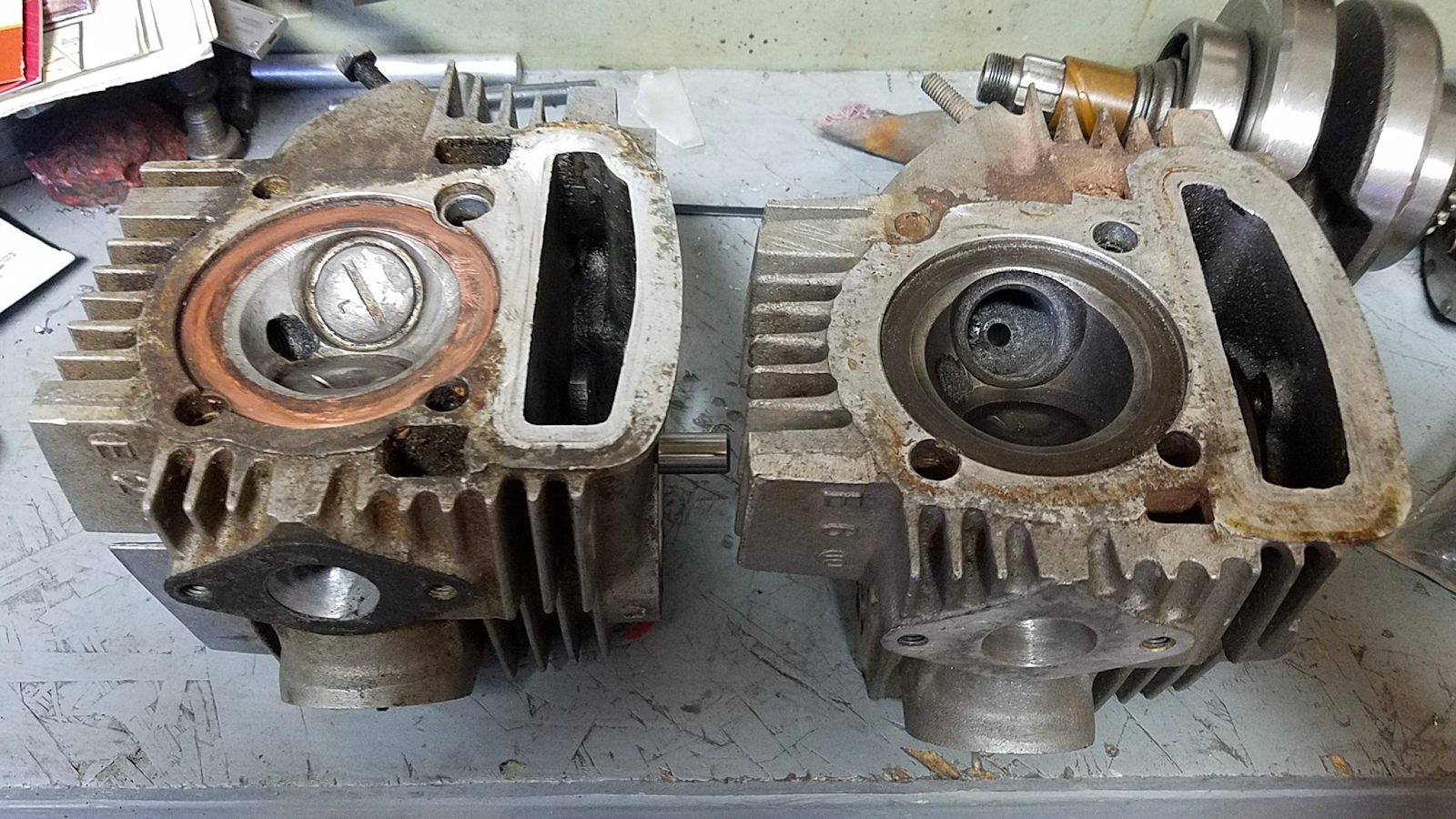
left: CT90 aluminium head next to an earlier "iron skulled" version / right: Honda redesigned the cylinder at the same time as introducing the all-aluminium head and the thicker cylinder walls of the new version (shown on the left of the picture) necessitated a new copper cylinder head gasket with notches to avoid the cylinder head studs. These changes mean that the newer aluminium head is not compatible with the old cylinders used on the C90s.
Aluminium-alloy pistons
Aluminium also plays an important role in piston design, since pistons absorb a lot of heat from combustion and therefore must conduct heat efficiently so that it can be rapidly transferred to the cylinder where it can be dispersed to the air flowing over the engine.
In 1913 W. O Bentley was looking to promote the sporty DFP (Doriot, Flandrin & Parant) cars he was importing from France and - with a view to improving performance and winning some speed records - had started to experiment with the use of aluminium-alloy pistons[4].
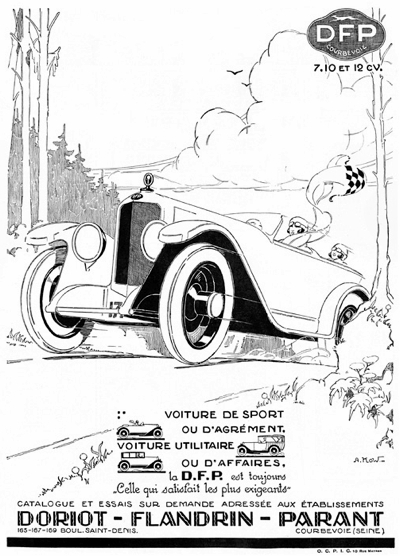
Combustion temperature inside the cylinder can reach over 1500C and, since aluminium will melt at around 600C, it was thought for a long time that aluminium-alloy would not be strong enough for this type of application. What Bentley and other early users of aluminium-alloy pistons were able to show was that the high thermal conductivity of the metal was so effective at dispersing heat that aluminium's relatively low melting point was never reached.
These improvements in temperature control allowed Bentley to increase the DFP's engine compression ratio - which increases power, but also temperature - without suffering from knock-related engine damage. By 1914 he had been able to raise the power of the 2 litre DFP engine far enough to set a new 89.7 mph record for a flying mile at Brooklands, a 50% improvement on the record set only a couple of years earlier.
Bentley joined the Royal Naval Air Service at the outbreak of the first world war and convinced them to adopt aluminium pistons in their aeroplanes. The new engines were a great success and used in a number of important British aircraft, including the Sopwith Camel.
Pistons
Soichiro Honda, the founder of Honda and designer of the Super Cub, joined ART Co. ltd - an automobile service shop founded in Tokyo in 1917 - as an apprentice in 1922. A few years after Honda joined, ART started to make racing cars and Honda was a keen contributor, assisting with design, engineering and driving. During this period ART also started to produce pistons and were the first company in Japan to create aluminium-alloy pistons.
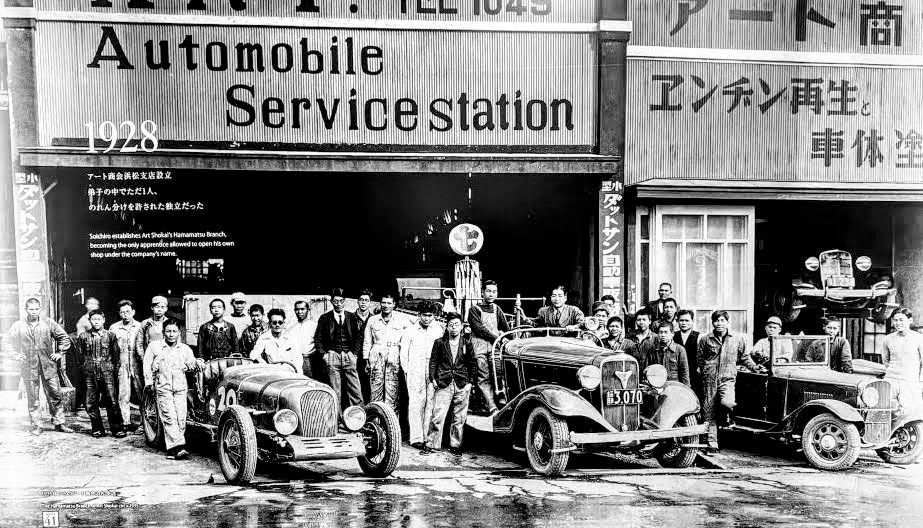
ART went on to make the pistons for Honda, including those used in the super cubs.
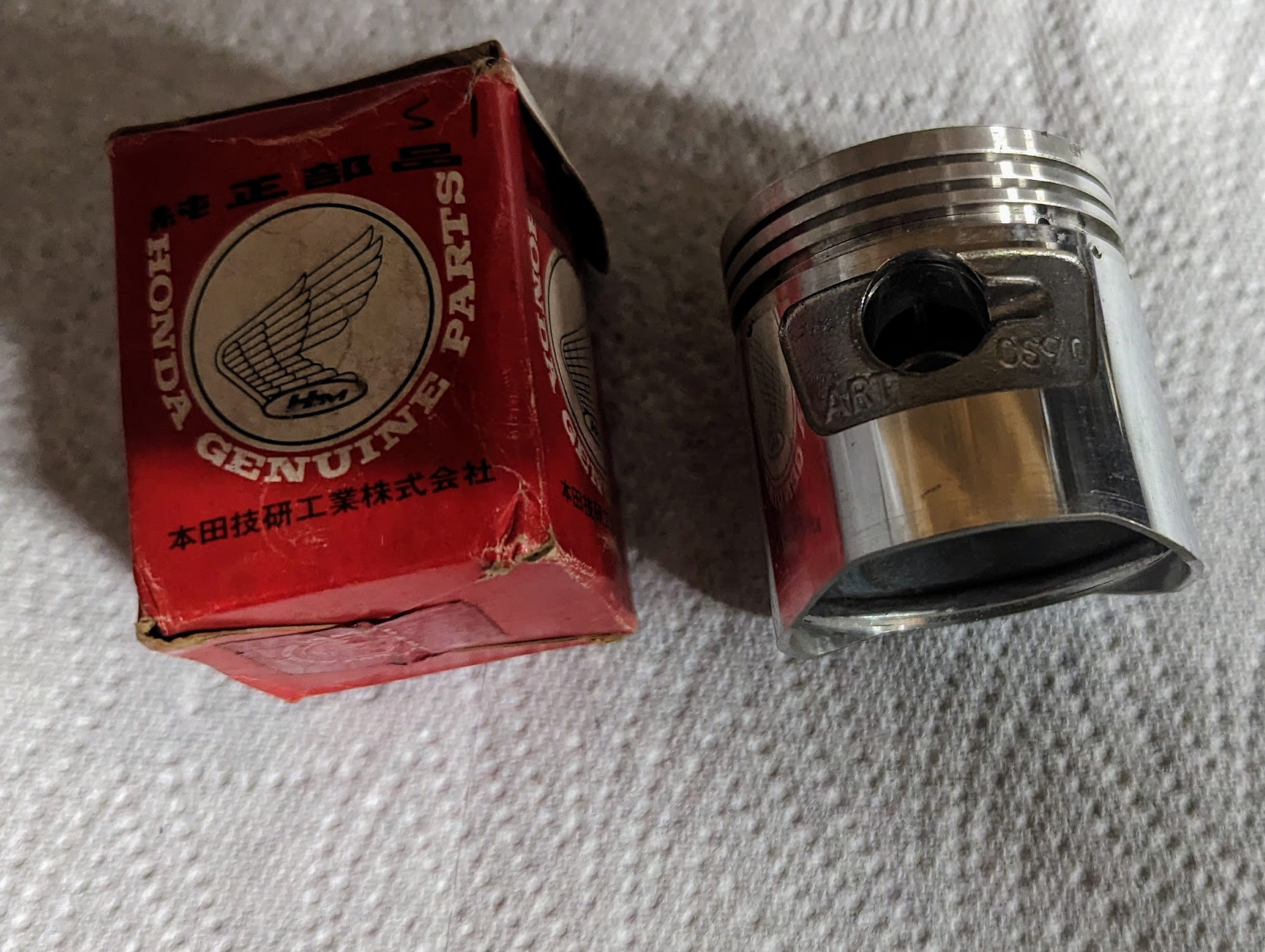
Piston rings
There are three piston rings: the top and second rings seal the combustion chamber and the oil ring scrapes the oil from the cylinder wall. The rings are a key route to transfer the heat of the piston to the cylinder walls where it can be dissipated through the cooling fins. They are made of a special iron alloy that resists wear and heat and the top ring - which is exposed to the greatest temperatures - is plated with a hard chrome finish for additional protection.
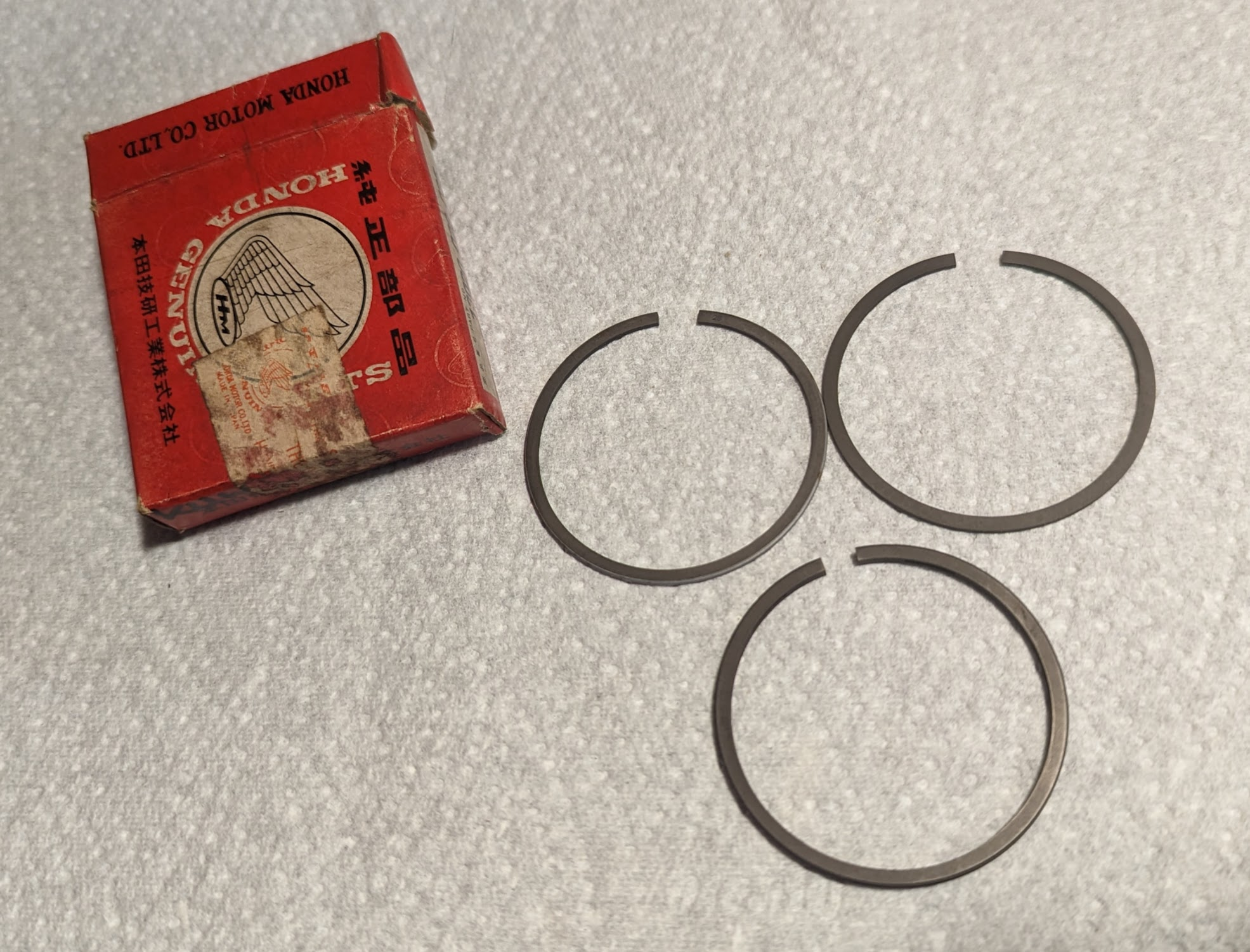
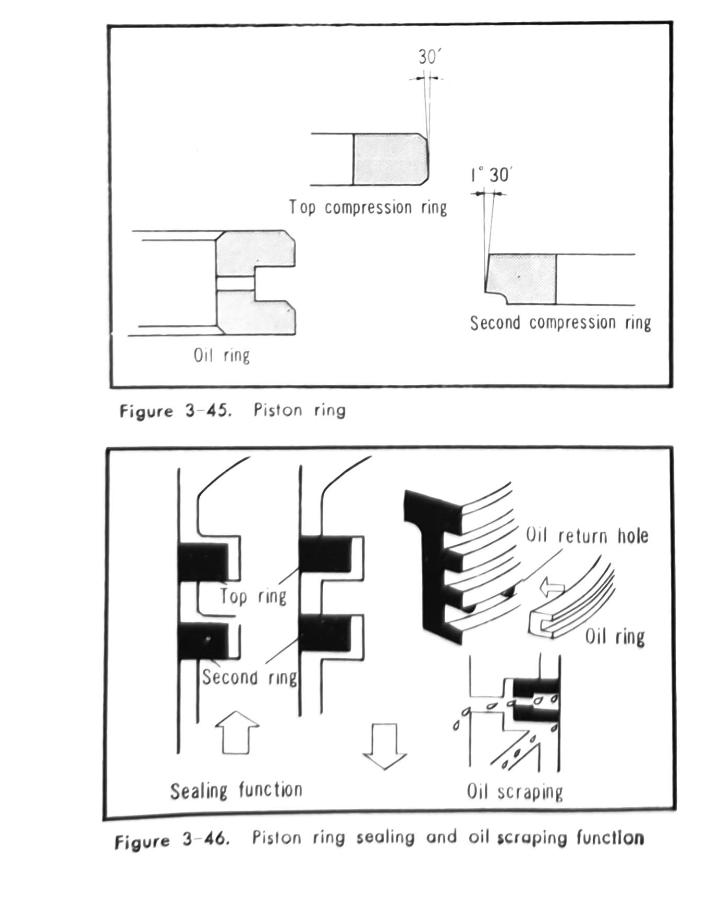
the diagrams shows the sealing and oil scraping function of the rings
As shown in the diagram above, the compression rings have a tapered face and must be fitted the correct way up:
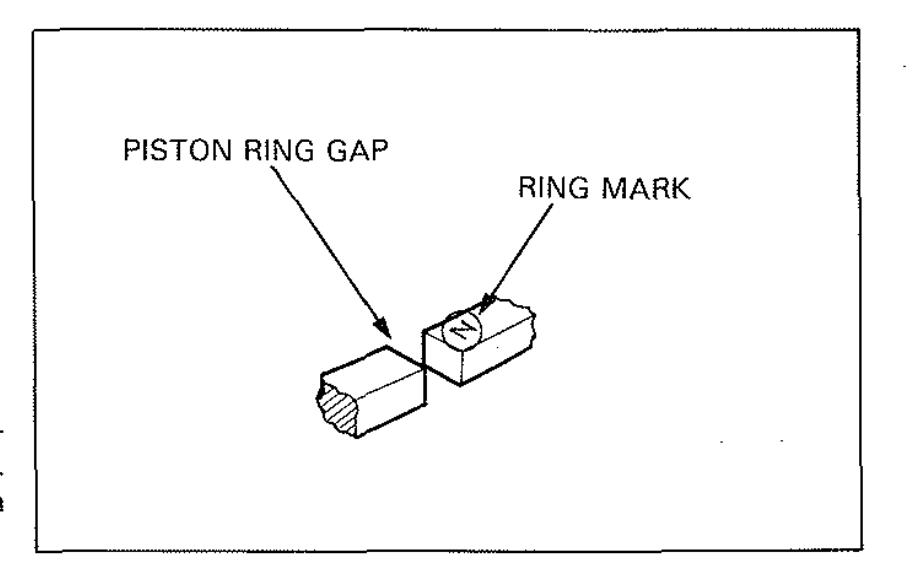
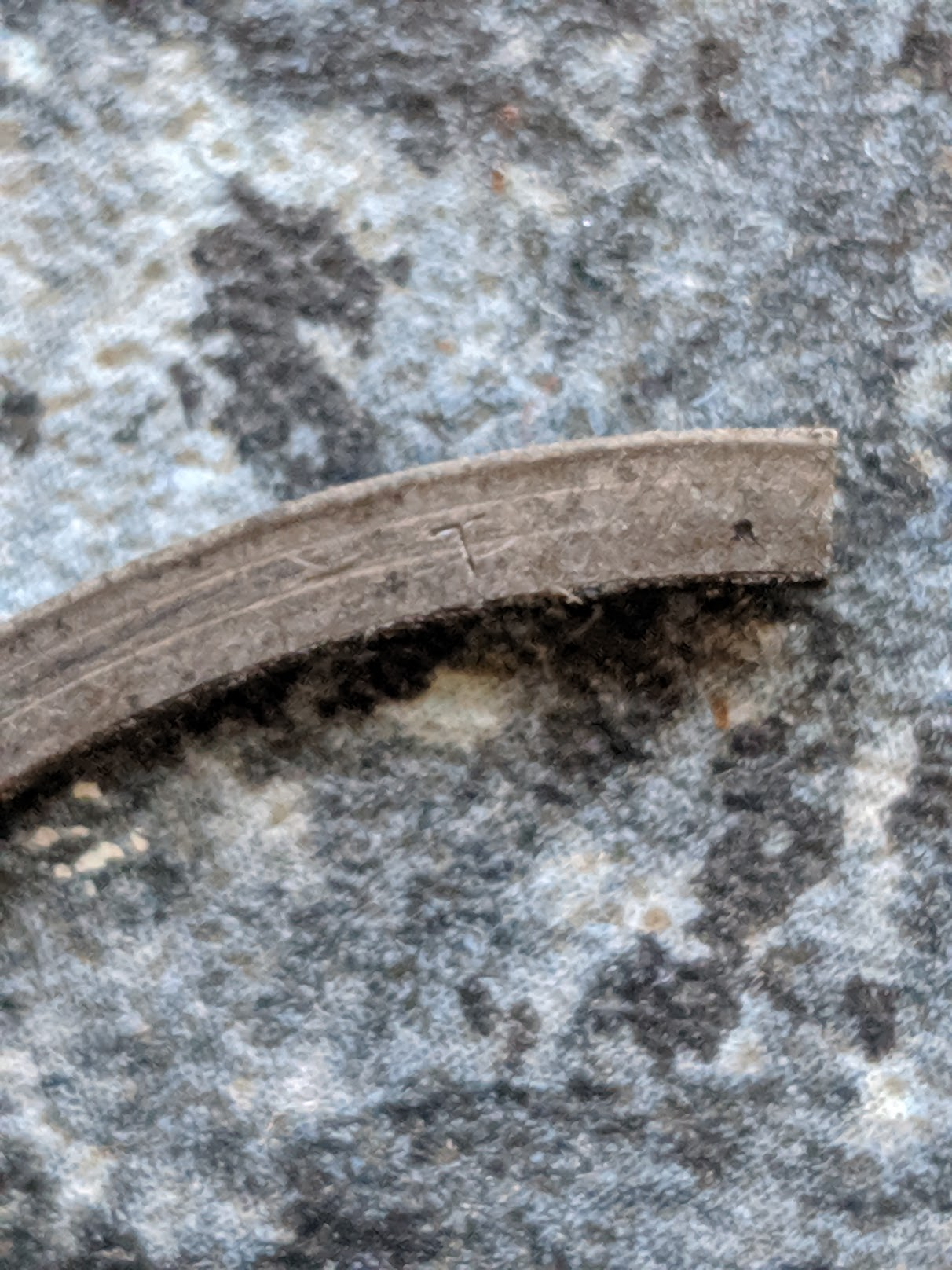
The original Honda piston rings are etched with the first letter of the manufacturer's name on the surface that should face up towards the top of the piston
The oil ring is needed to remove oil from the cylinder wall. If the oil ring fails, oil flows into the combustion chamber and burns, causing smoke. The oil ring is either of a split type arranged with two side rails and a slotted expander, or an single piece type with a slotted square edge (both types were used on the 90 engines, depending on when it was produced).
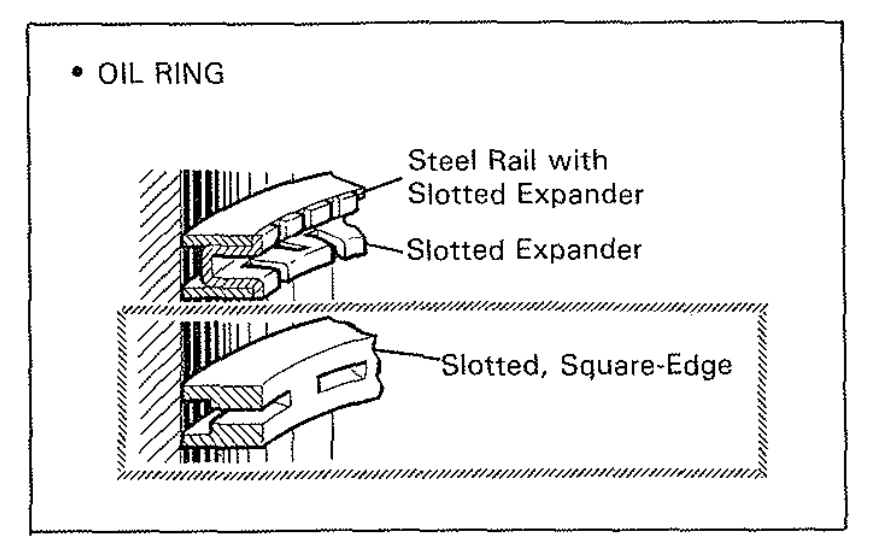
Piston ring end gap
The piston ring end gaps must be correct else the rings can bulge against the cylinder walls as they expand with heat, or - if the gap is too large - they won't seal properly. The Honda manuals show this gap being measured with the ring at the top of the cylinder and also at the bottom. The usual advice is to place the ring part way down the cylinder the measurement is being take where the ring resides in normal operation. The OEM rings should be pre-gapped, but per the manual you should check anyway.
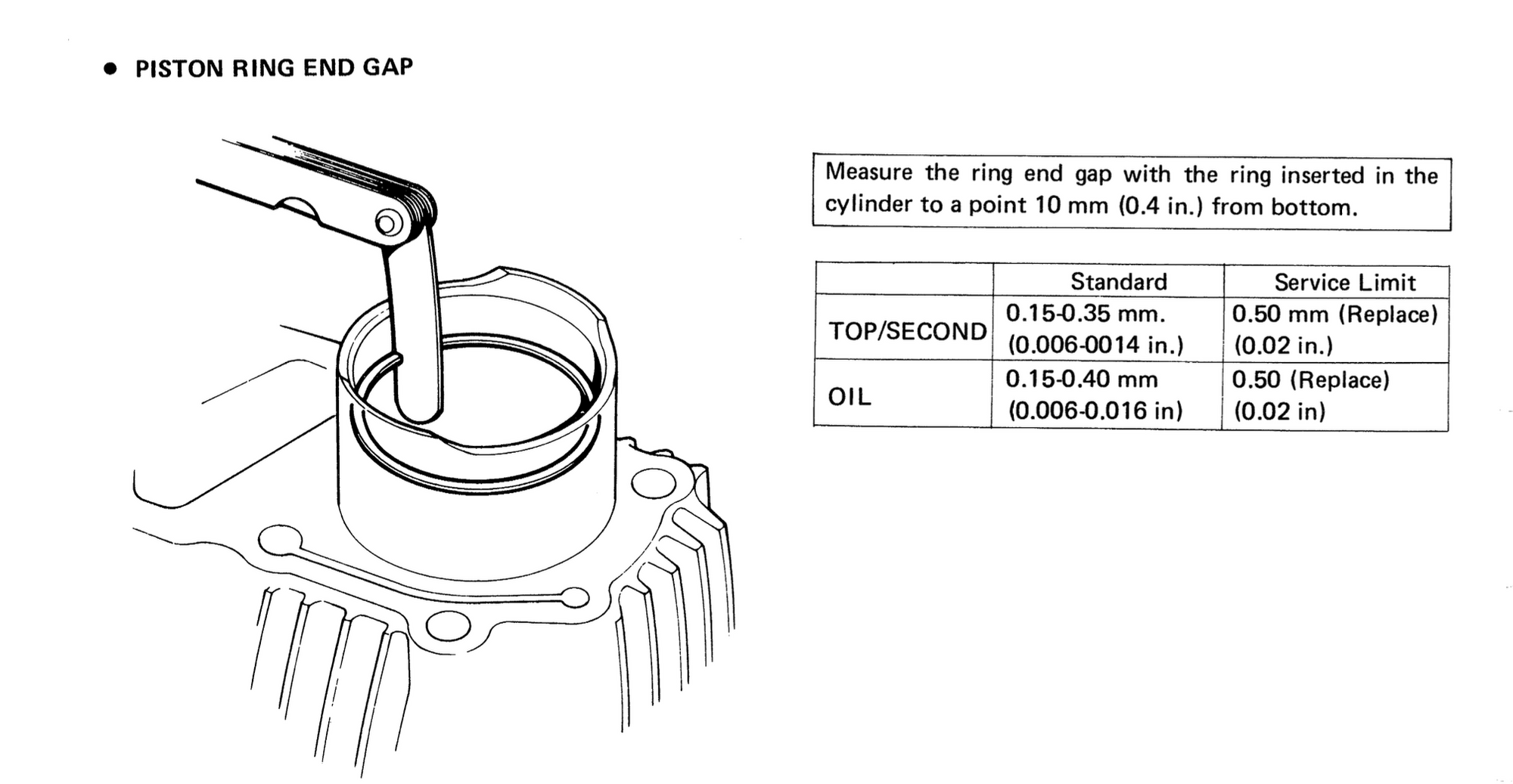
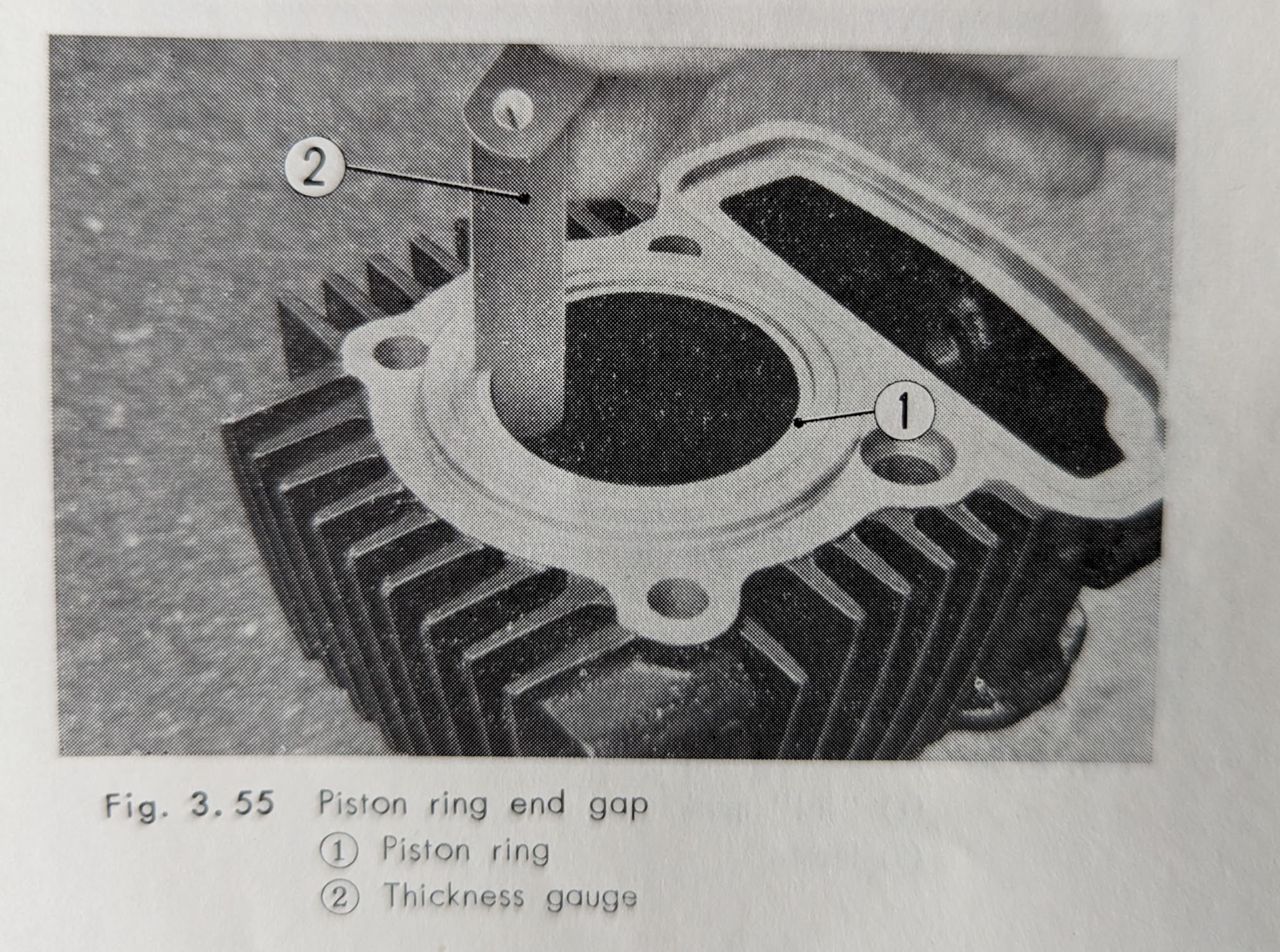
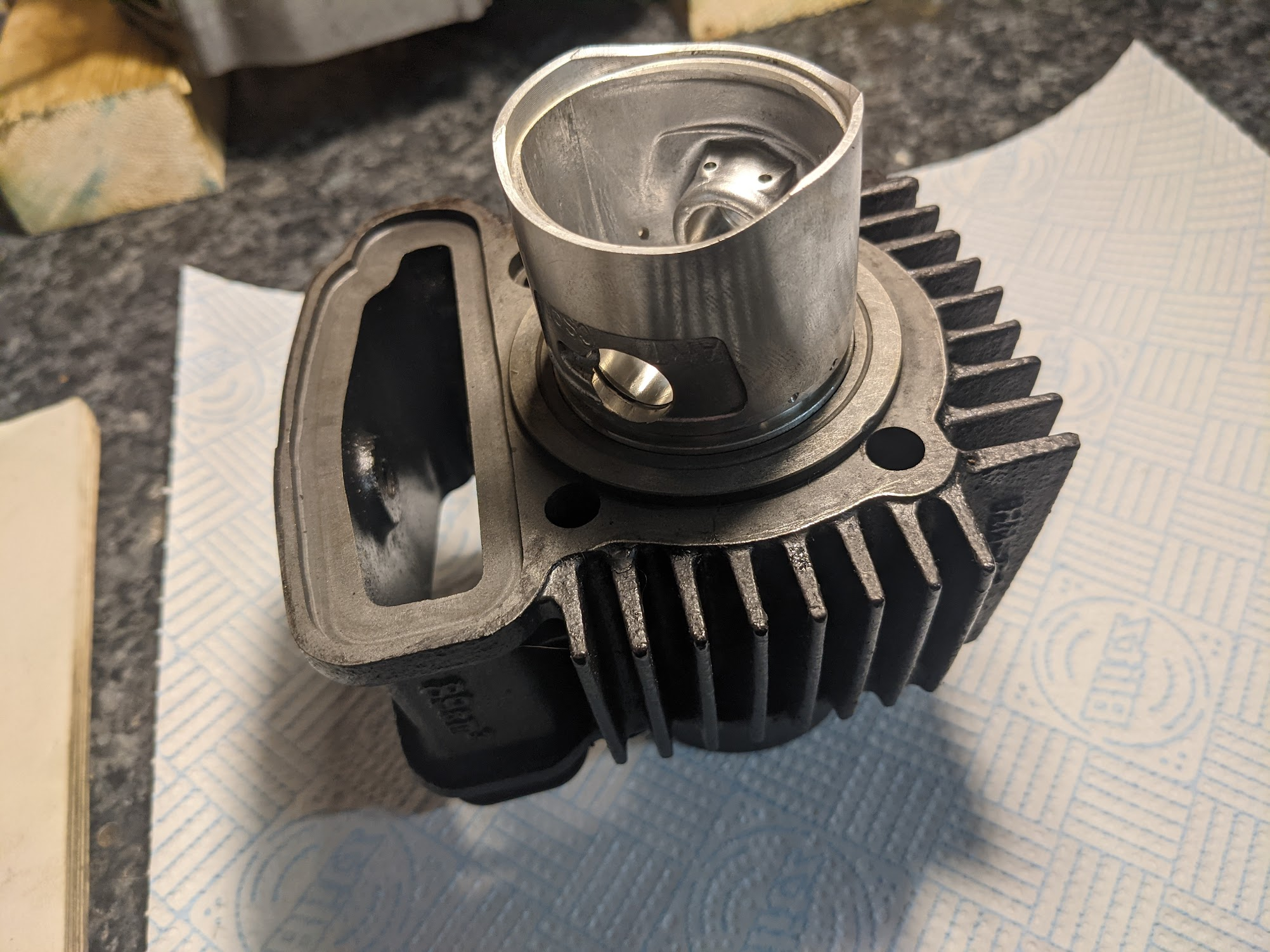
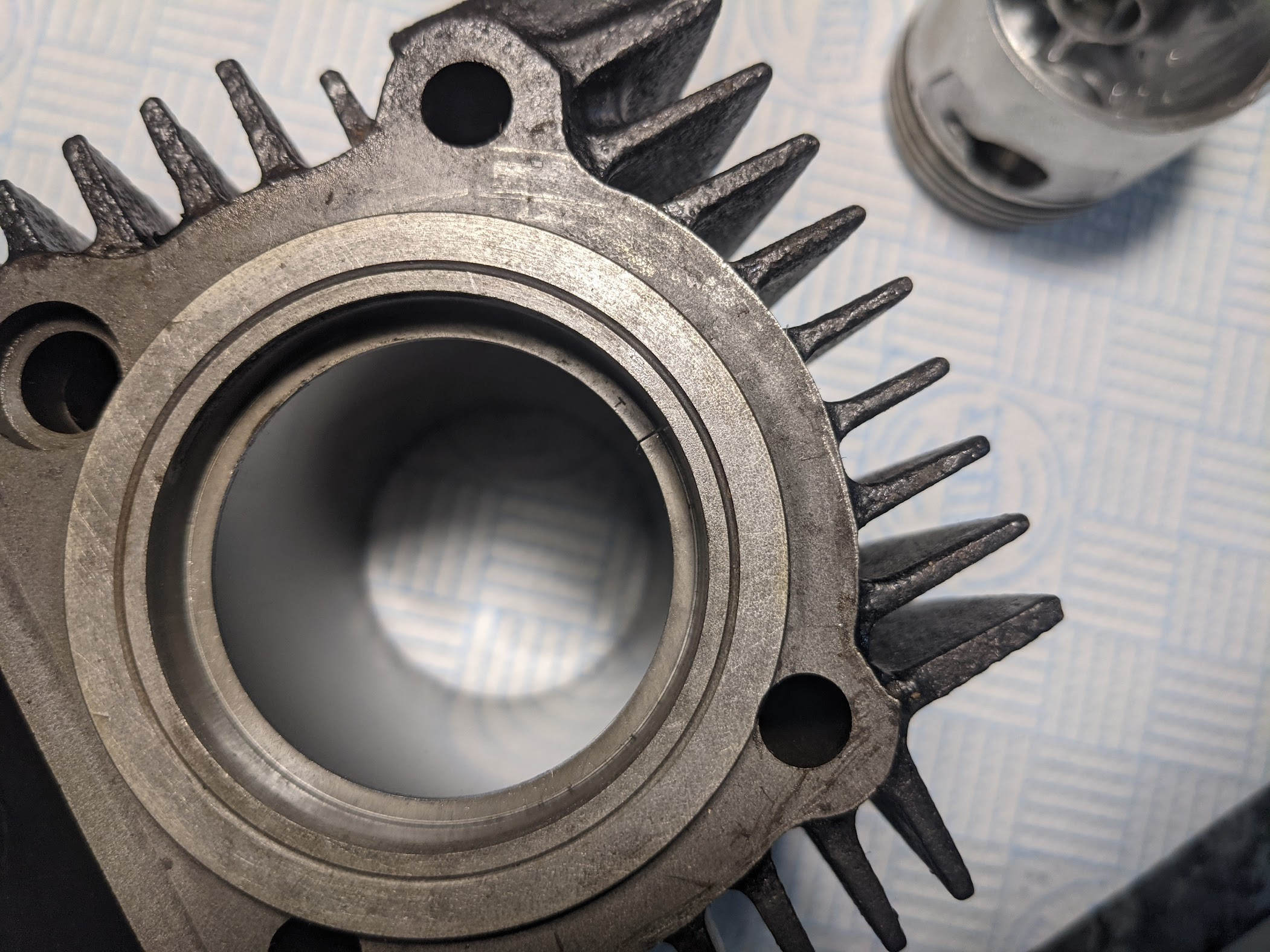
you can use the piston to ensure the ring is level in the cylinder before measuring the gap. A thin file can be used to increase the gap if necessary
Piston stroke
The stroke of this engine is 45.6mm. You can read more about how the piston and crank are connected here
Cylinder
In the C90 the piston is housed in a cast iron cylinder. The early versions of the sporty s90, which was based on the same engine as the C90, came with an alloy-finned cylinder with an iron sleeve along with an all aluminium alloy head and a go-faster cam shaft - all measures to reduce weight and increase power while keeping the engine at a safe temperature.
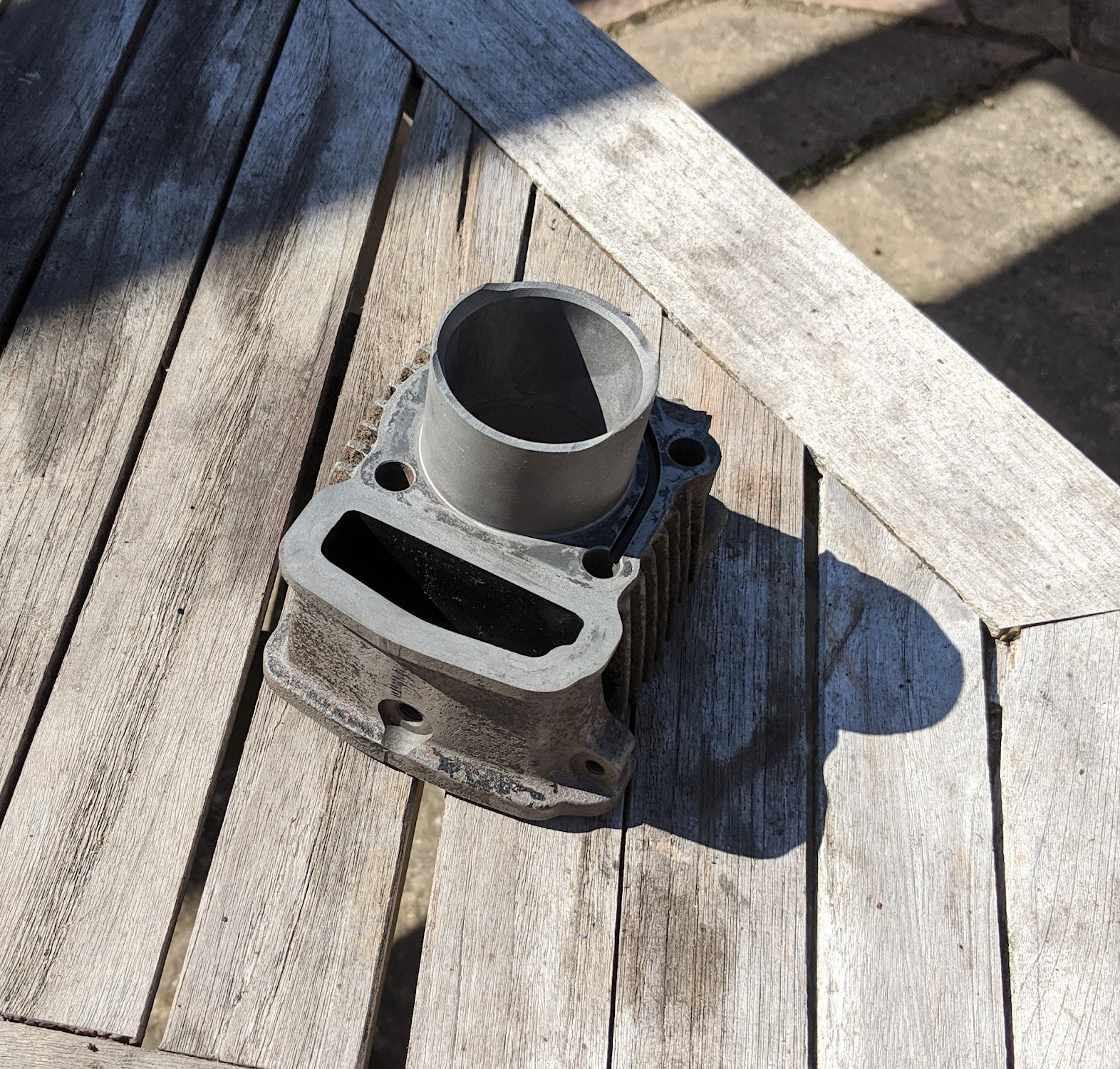
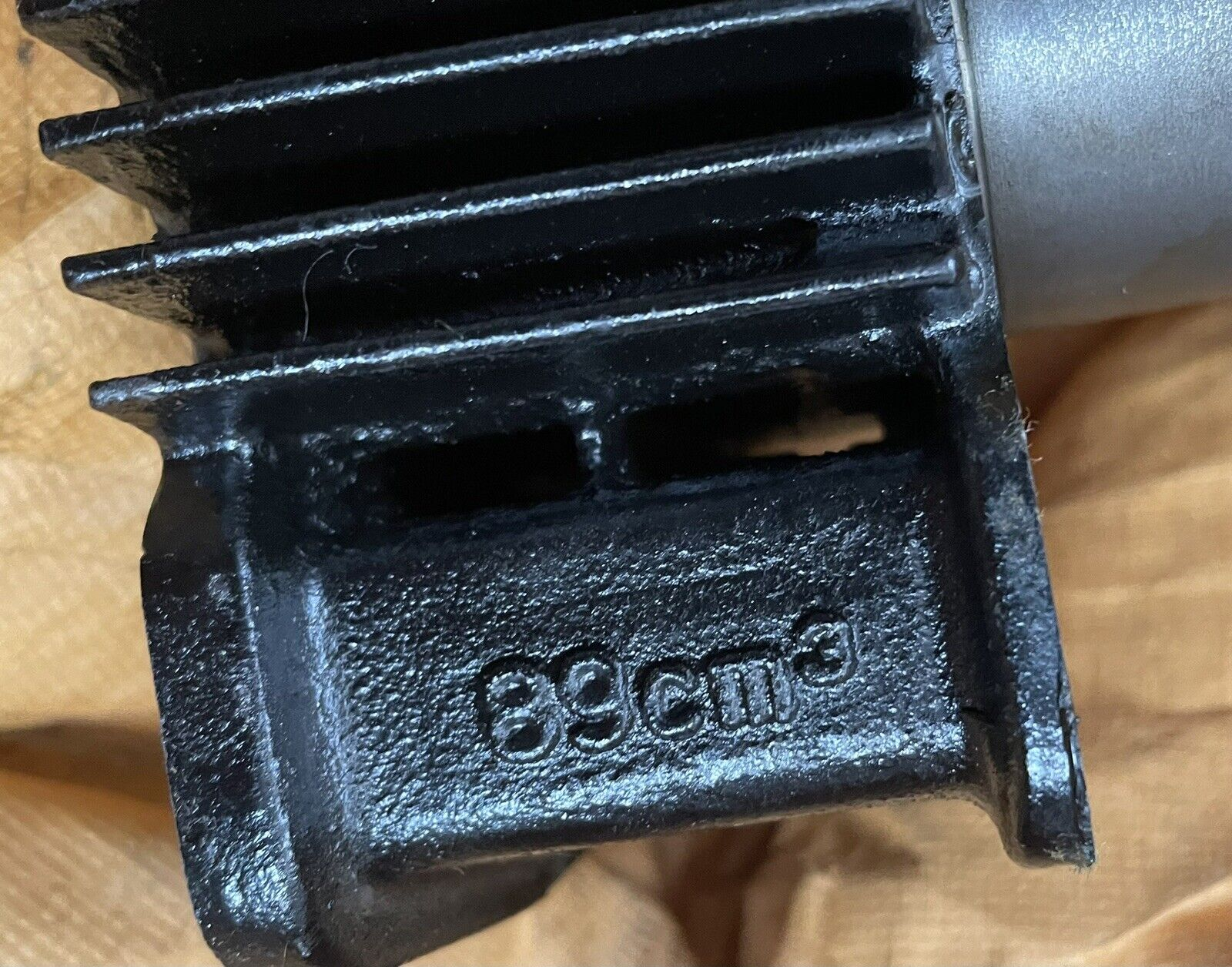
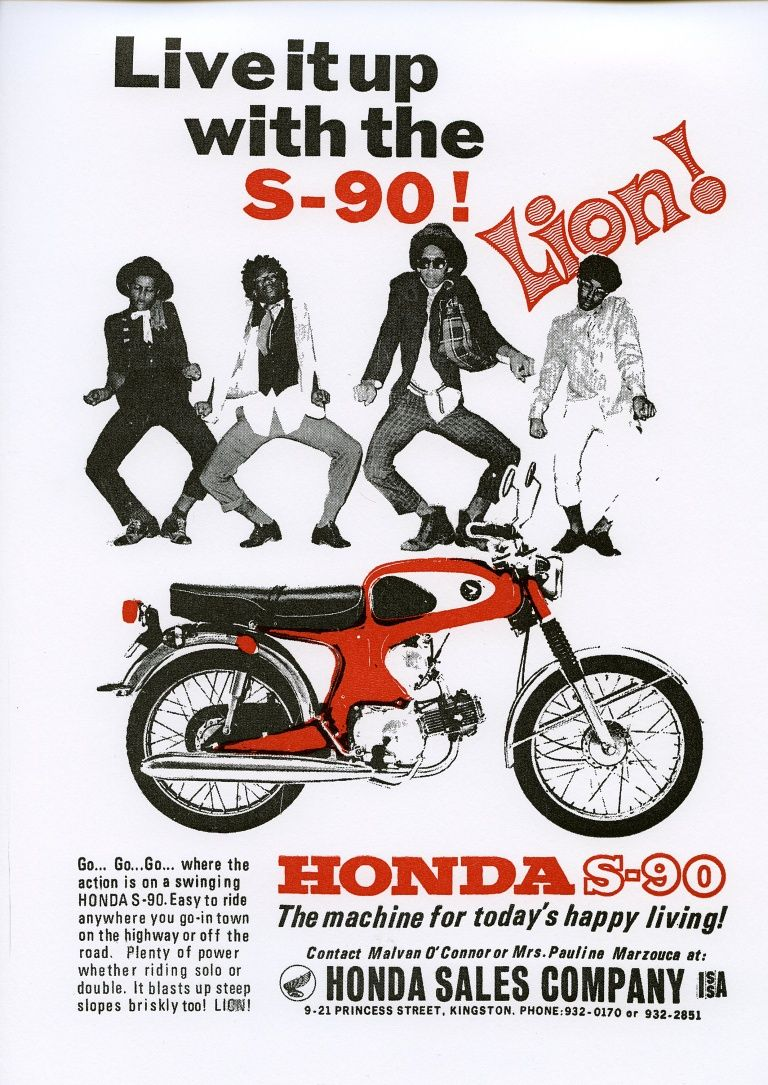
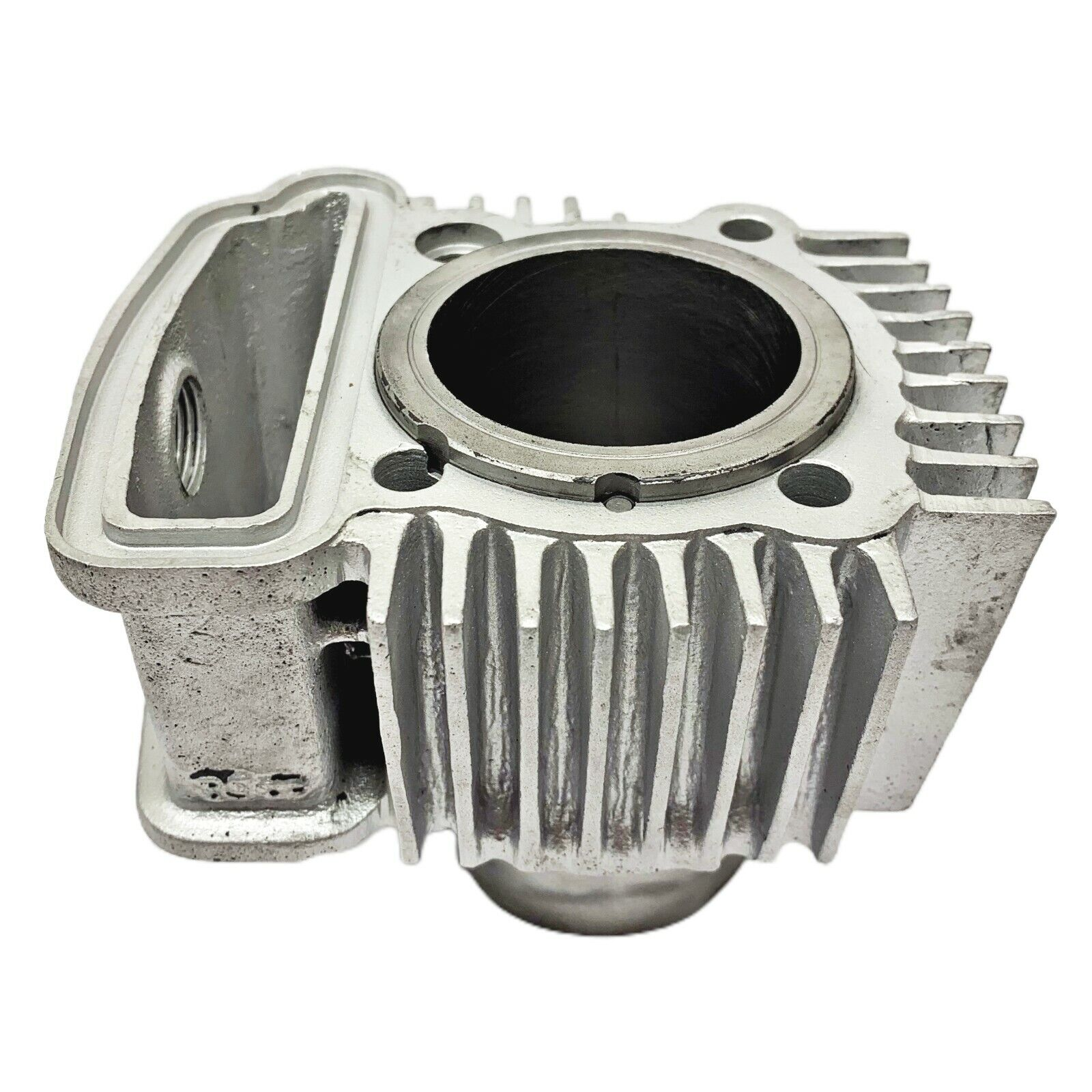
standard c90 cylinder (top) / the legendary S90 with its fancy cylinder (bottom) developed 8bhp and could top 60mph
Piston seizures
We know from the Honda manuals and service bulletins produced at the time these bikes were made that heat is the primary cause of piston damage. Honda identifies a number of maintenance activities that, if neglected, can cause over heating, including wrongly adjusted valves and ignition timing, incorrect fuel/air mixture and the use of spark plugs with the wrong heat range:
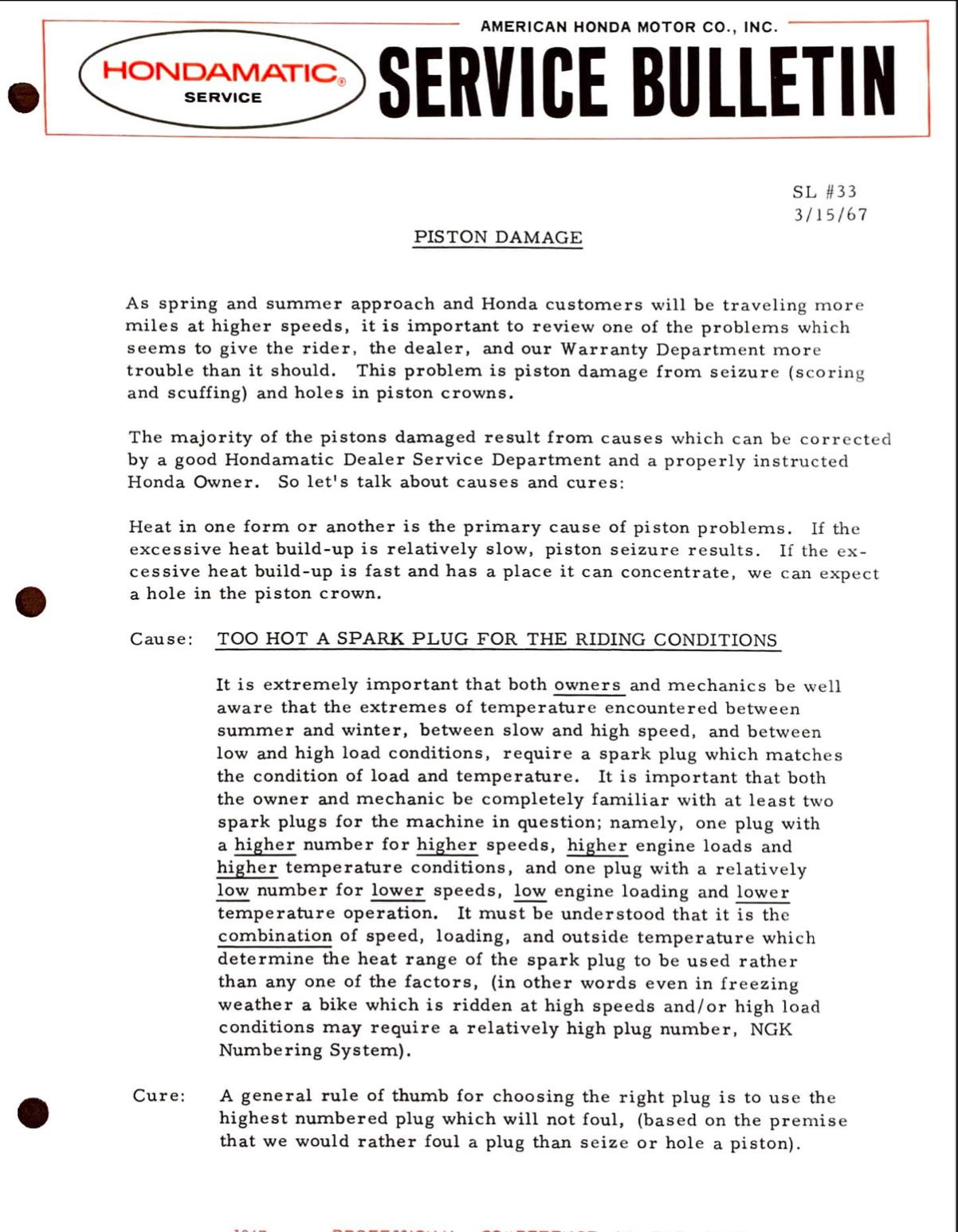
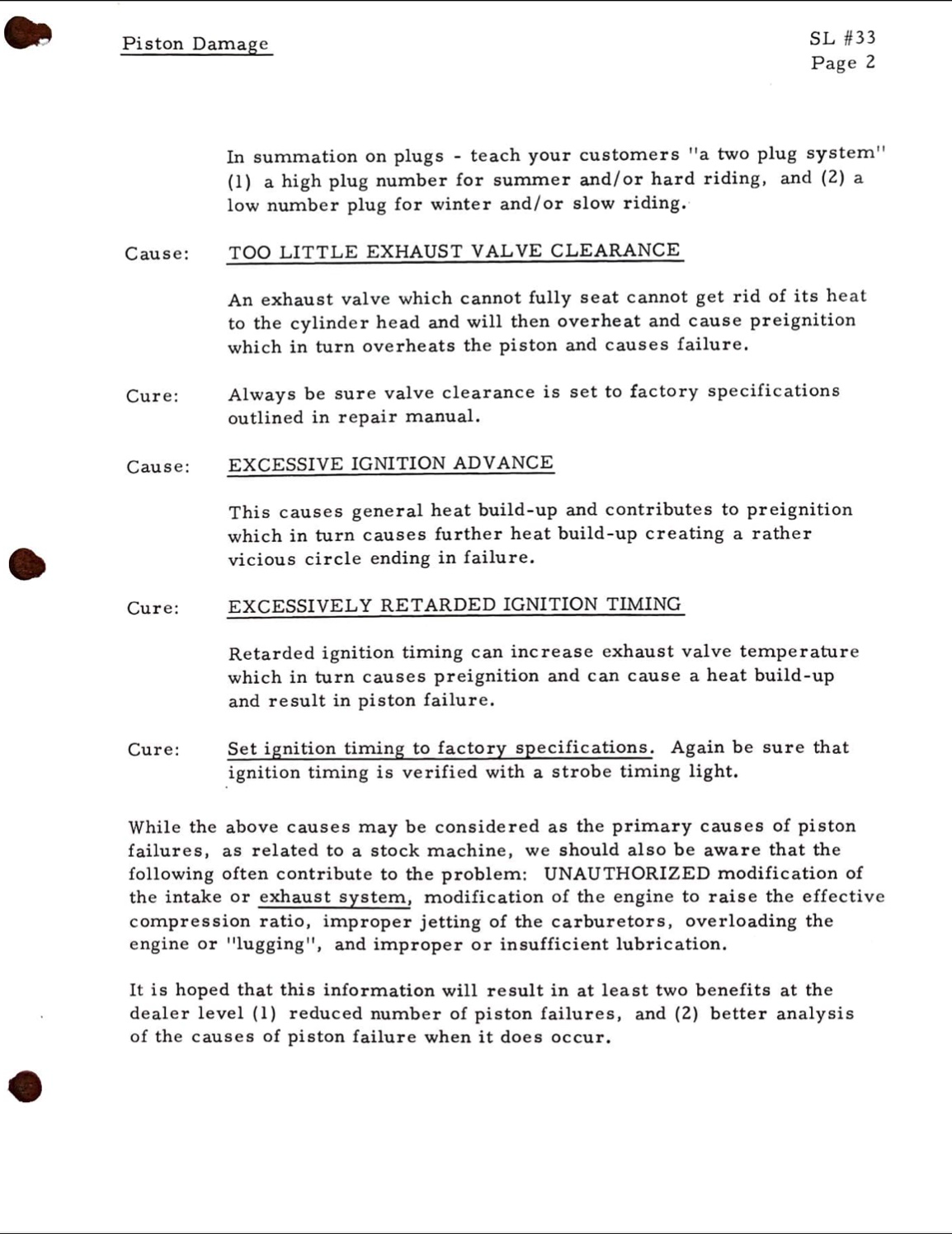
I suppose that ignition timing is the most interesting from the perspective of the 6v C90s unfortunate reputation for seizing up, since this was one of the problems resolved in the subsequent 12v model which used CDI instead of points to time the ignition.
Another culprit may be cam-chain maintenance: unlike the 12v engine the cam chain tensioner in most of the 6v engines require periodic manual adjustment. The tell-tale signs that this maintenance has not been done are that the the tensioner retaining screw nearest the chain is damaged as the chain flaps about and the teeth on the oil pump drive sprocket get worn away as the chain skips teeth.
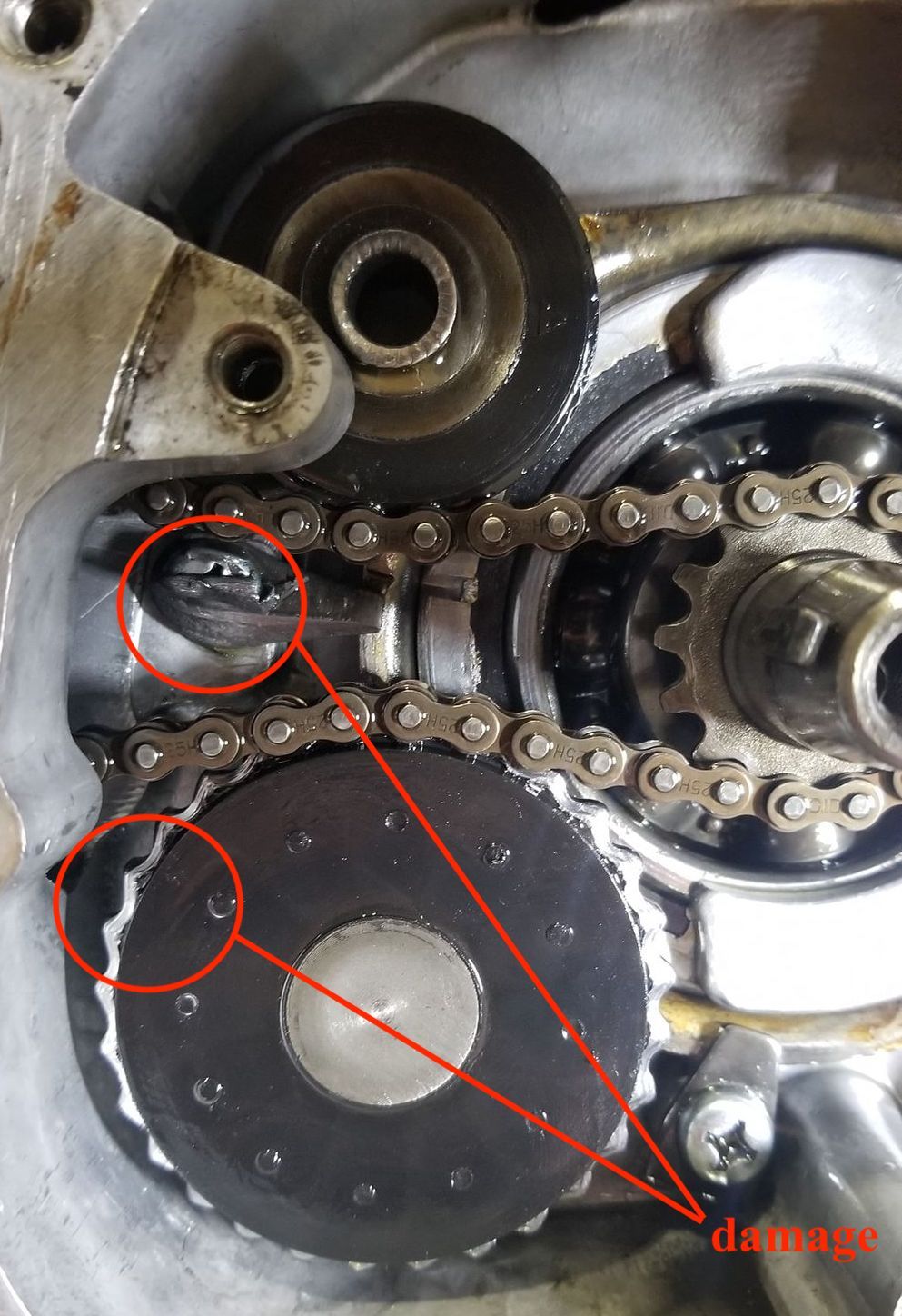
I think this must have two impacts:
- The chain can slip on the oil pump drive socket, reducing the amount of oil pumped to the crankshaft and thus limiting the amount of oil sprayed on to the cylinder walls and piston
- As the tension on the stretched chain will vary with engine running conditions so will the point at which the camshaft-mounted contact breaker points opens and this will result in eratic ignition timing
... a double-whammy of potential overheating problems.
The final factor is probably the most obvious: these engines hold less than a litre of oil and it needs to be kept topped up and changed regularly to prevent lubrication failures. It is also important to keep the oil strainer clear since, when blocked, it will restrict oil to both the cylinder head and also to the piston, connecting-rod and transmission (you can read more about the lubrication system here).
Over sized pistons
When cylinders are outside of the service limits due to wear or because of damage following a piston seizure they can be rebored.
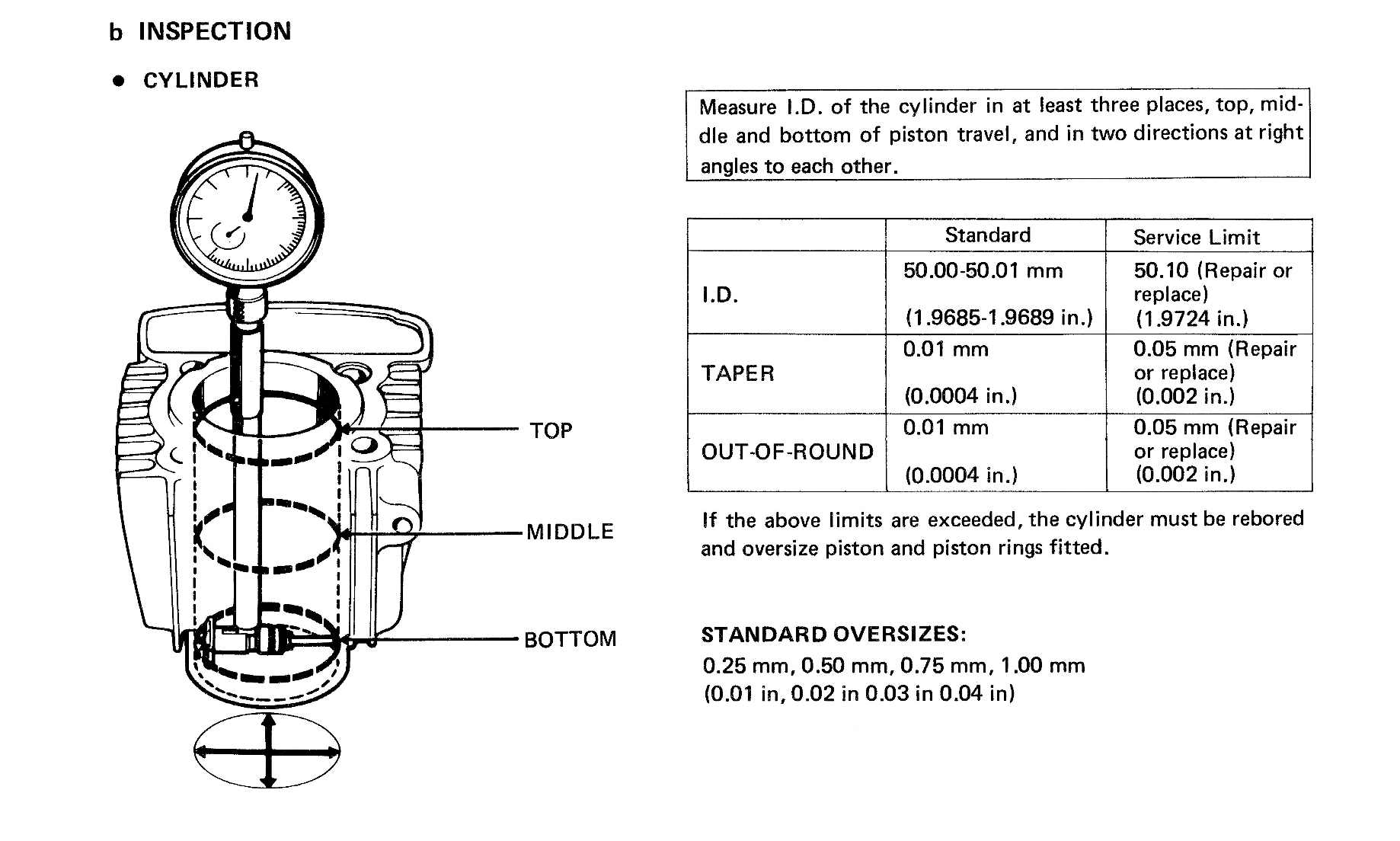
Oversize piston and piston rings are available in four sizes for the C90: 0.25mm, 0.50mm, 0.75mm and 1mm.
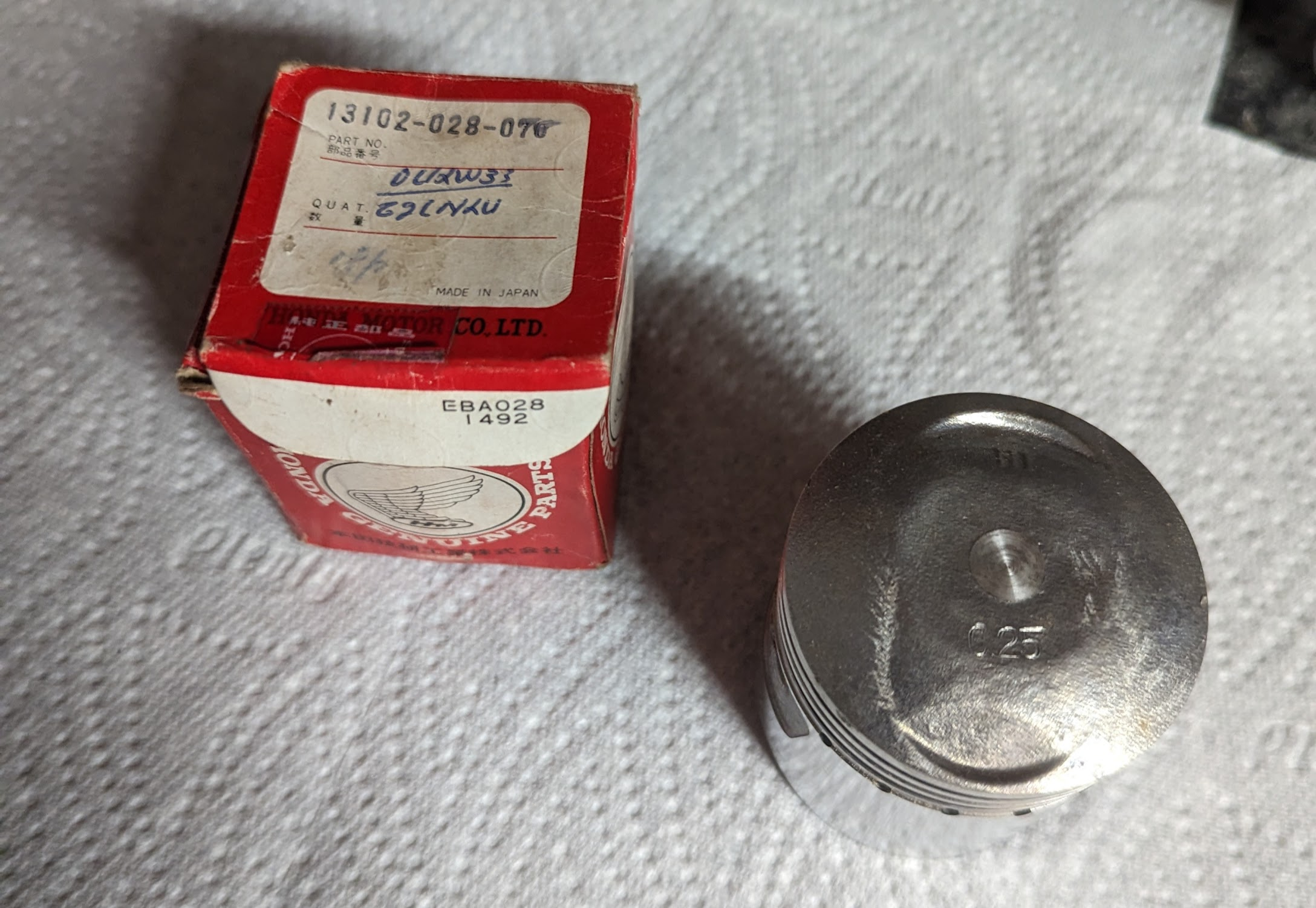
You can read about how to measure the cylinder in this article.
Crankcase breather
The reciprocating motion of the piston combined with any blow-by of combustion products that pass the piston rings causes the interior of the crank case to be under continuously varying pressure. The pressure is relieved through two crank-case breathers.
The hot gasses pass through a baffle in the right hand crank case and enter the left hand side of the case via the vent shown at (A) below. The gases are then routed thought the left crank case cover and are discharged above the drive train (B).
Honda modified the left hand crank case design in the 1960s, adding a secondary breaker (C) lower in the case - this discharges behind the chain guard.
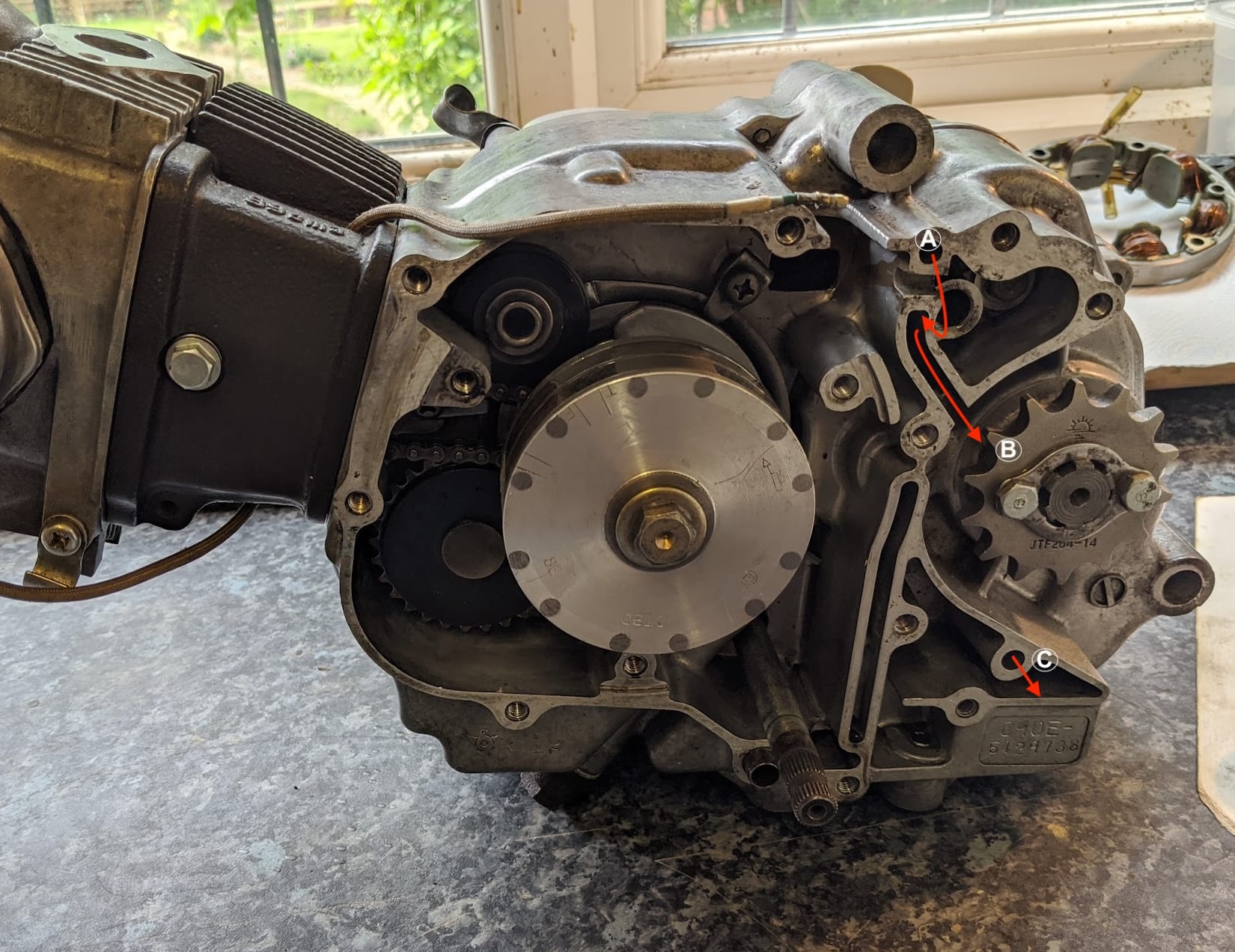
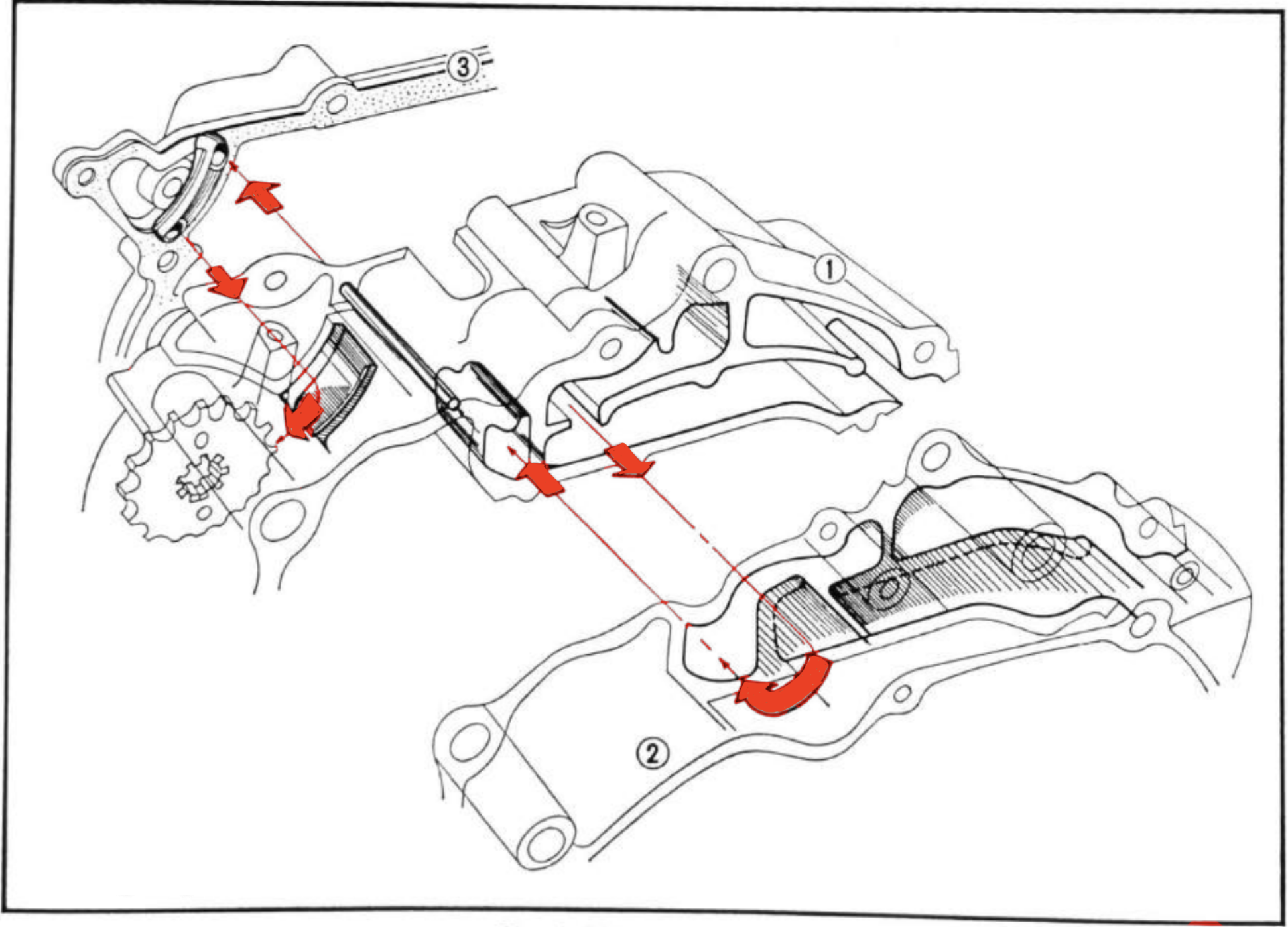
left: primary and secondary crankcase breathers / right: the route the gasses take in the primary breather system
Assembly
The piston is orientated with the "IN" marking facing up to the inlet port and the piston rings should be arranged so the end gaps are they are roughly 120° apart. Don't forget the o-ring on the stud that carries the oil to the cylinder head.
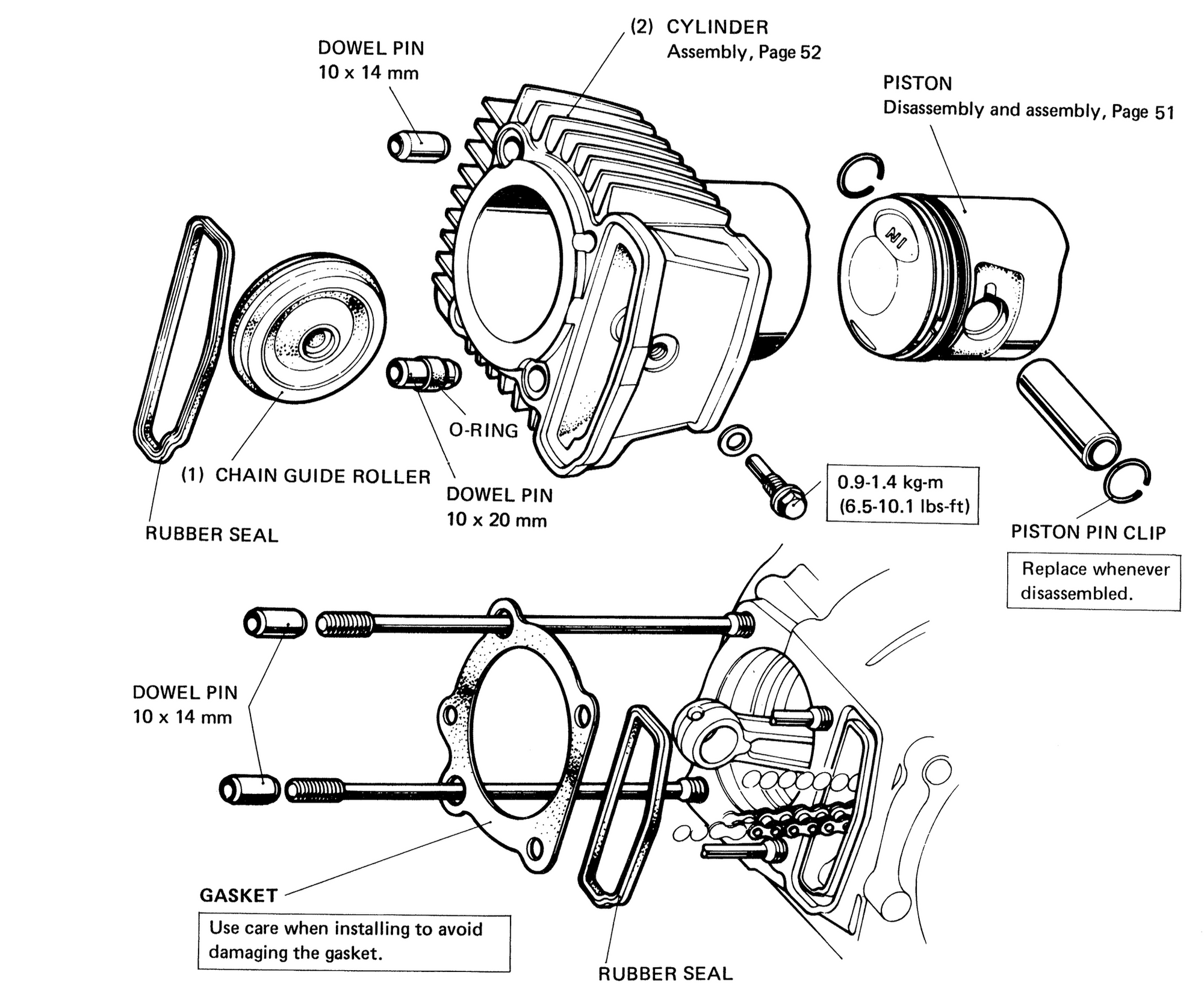
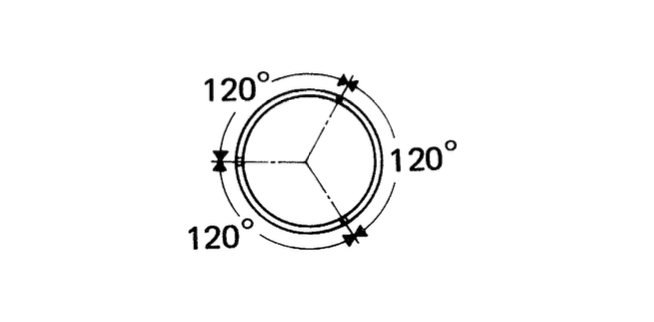
assembly (left) / ring spacing (right)
There a couple of other considerations when installing your new piston or piston rings that have a bering on how the new parts bed in with use. As with a lot of the discussions related to running-in newly assembled engines it is hard distinguish old wives tales from the facts, but here goes...
oiling rings and cylinder
There is a school of thought that says you should not oil the cylinder or piston rings on assembly. The gist of the thinking is that doing so somehow improves or accelerates the bedding in of the parts, presumably because there will be direct metal-to-metal contact between the piston rings and cylinder for a period when you first run the engine.
It is up to you whether you think this is a good idea - all I can add is that Honda specifically say to apply oil, so that is what I did too:
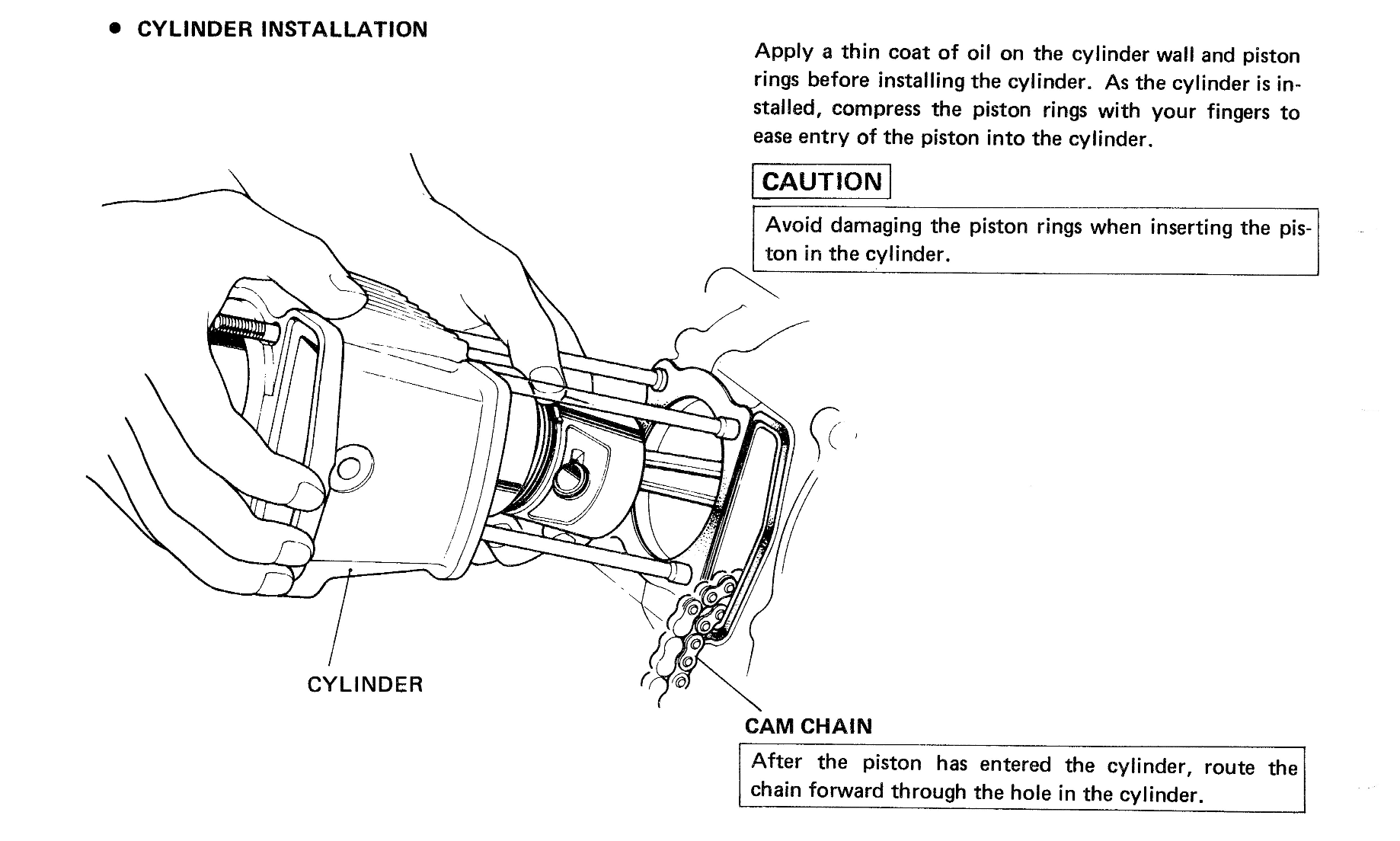
Honing
When you have a cylinder rebored the machinist initially runs a boring machine to establish a hole that is slightly undersized and then uses a second device - called a cylinder hone - to remove the machining marks left by previous process and to finish the cylinder to the final dimensions (hone in this context meaning "to finish"). The honing process leaves a tell-tale set of fine crosshatched scratches on the walls of the cylinder.
When fitting new piston rings in an old cylinder in which the original honing marks are no longer visible on the cylinder walls, some people argue it is a good idea to reinstate this scratch pattern before installing the new rings. An amateurish job of this can be done by running an inexpensive hone back and forward a few times in the old cylinder bore.
There seems to be general agreement that the scratches left by a proper cylinder hone have a role in retaining oil on the cylinder wall but despite a lot of reading I was not able to get to the bottom of whether it was necessary to reinstate the honing marks on old cylinder, nor could I find a clear explanation of why it might be a bad idea.
Honda don't mention it in the Super Cub workshop manuals so you will have to make your own mind up about it. In my case, I did decide to run a cheap hone through my C90 cylinder but I still don't know if it is the proper thing to do.
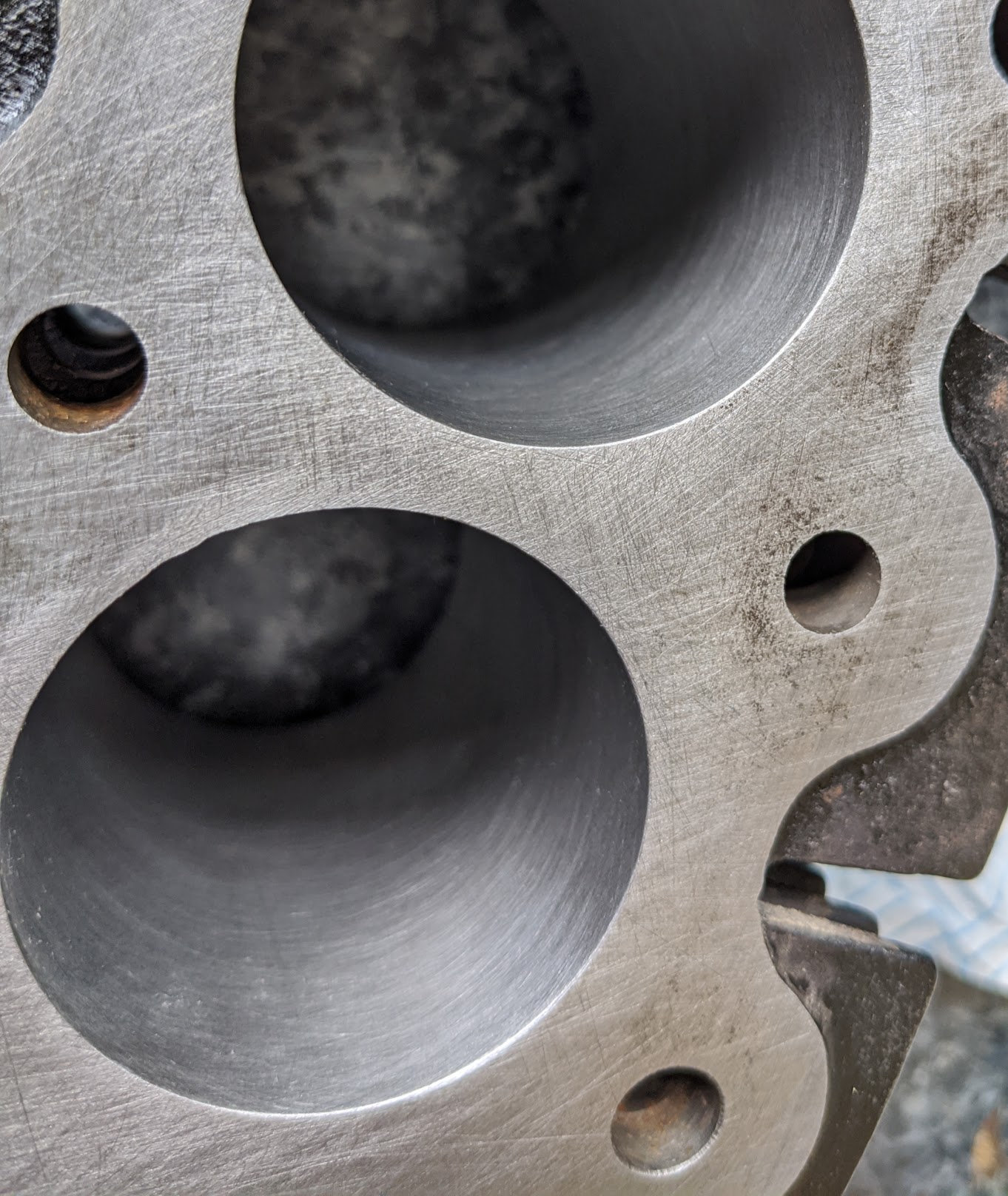
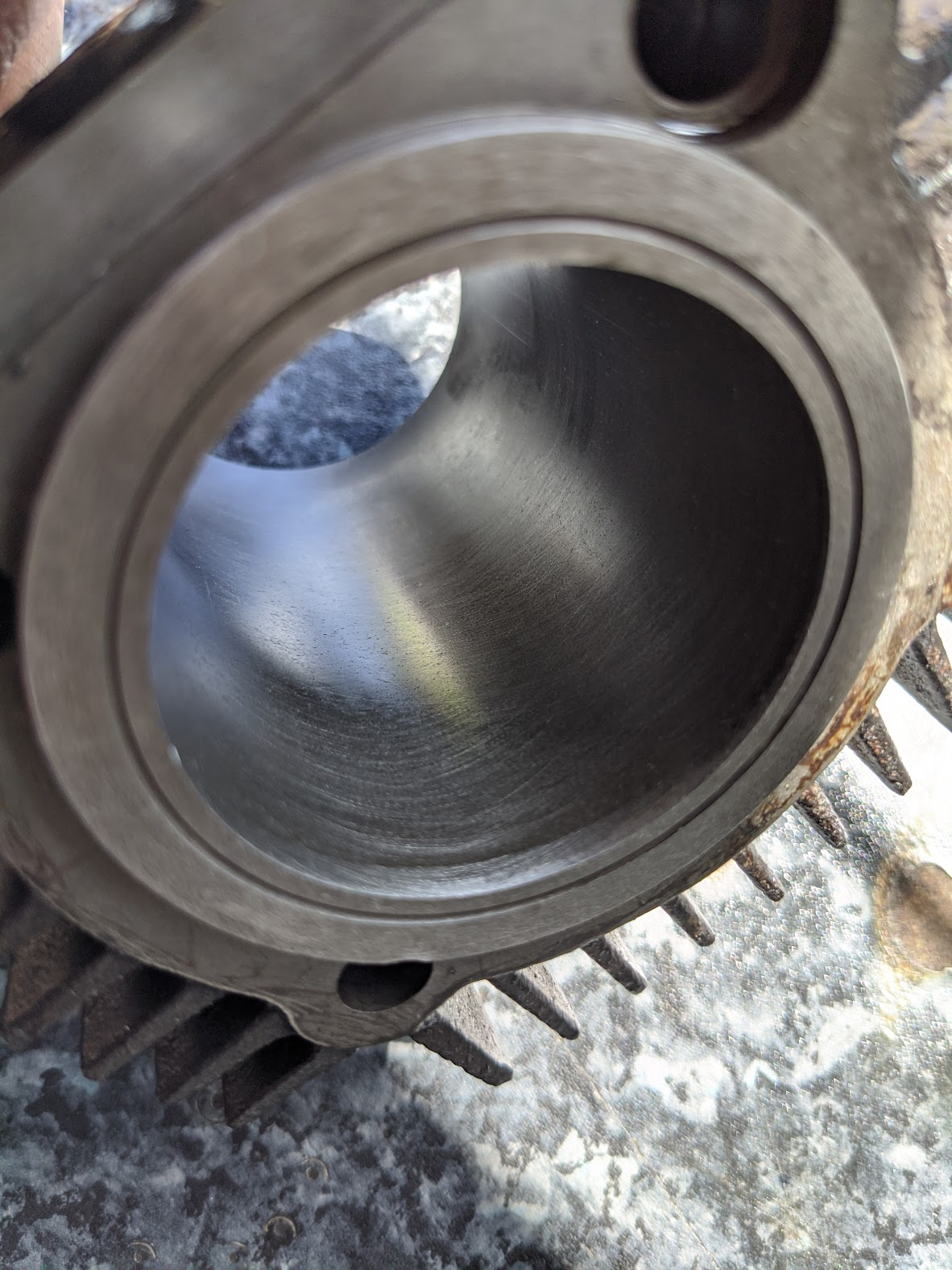
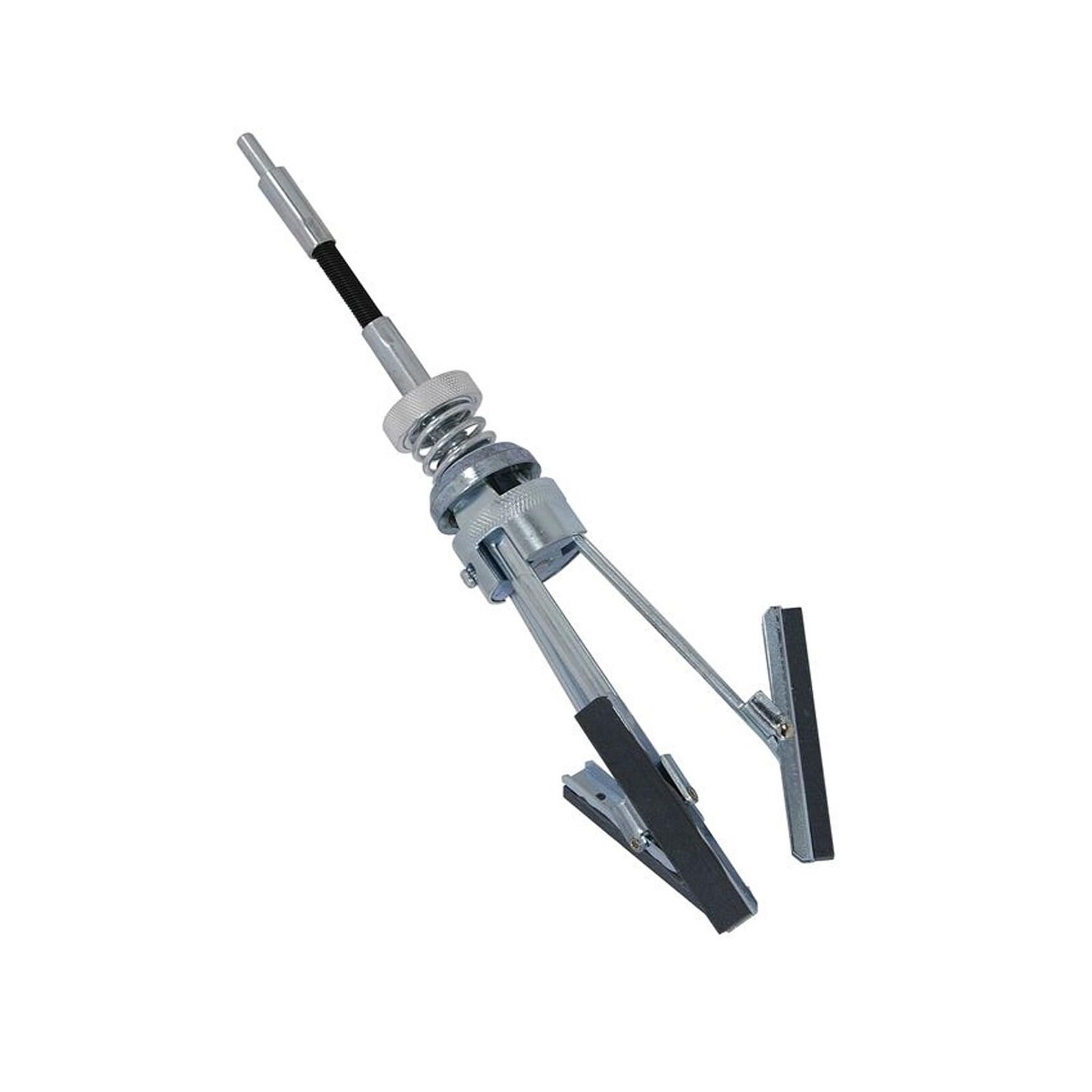
left: honing marks on a twin cylinder that I paid to be professionally rebored / centre: my ham fisted diy attempt on my c90 cylinder / right: the el-cheapo hone I used
*Edit* after writing this post I contacted the excellent Matt Huddson at The Dirty Garage (warning contains swears) and he gave me an admirably clear account of what is going on, which I've tried to summarise below:
- The hone marks help bed the rings into a new cylinder, as the clearances are tightest when new.
- Any wear after the initial bedding-in will make the cylinder wider than optimal
- As a result, when you are replacing the pistons rings on an old cylinder the fit will be relatively "sloppy" and honing marks are unlikely to be very beneficial
- the only way to really know whether boring or honing is appropriate is to accurately measure the cylinder
He also added that the cheap hone I used is not much good and that low powered air cooled engines tend to wear relatively slowly.
Cylinder head gasket
The copper gasket is reusable, although they do tend to harden due to the heat generated by the engine. A used gasket can be annealed (softened) by heating it to a dull red colour and then quenching it in cold water while hot.
I noticed that the after-market gasket originally fitted on my engine was thinner than the genuine version. I've no idea what difference this makes - other than a nominal increase in compression - but no doubt Honda made the original 0.5mm for a reason.
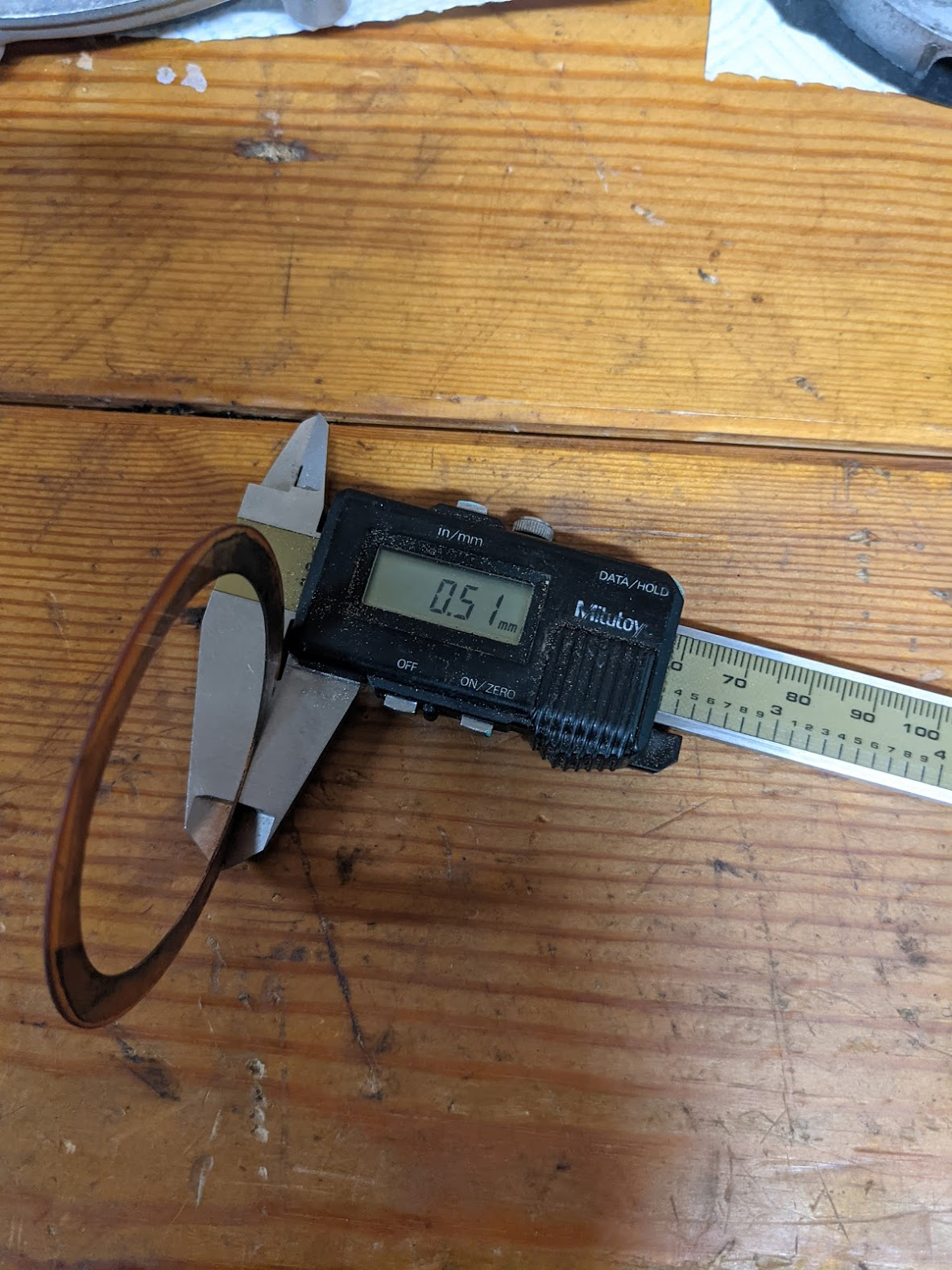
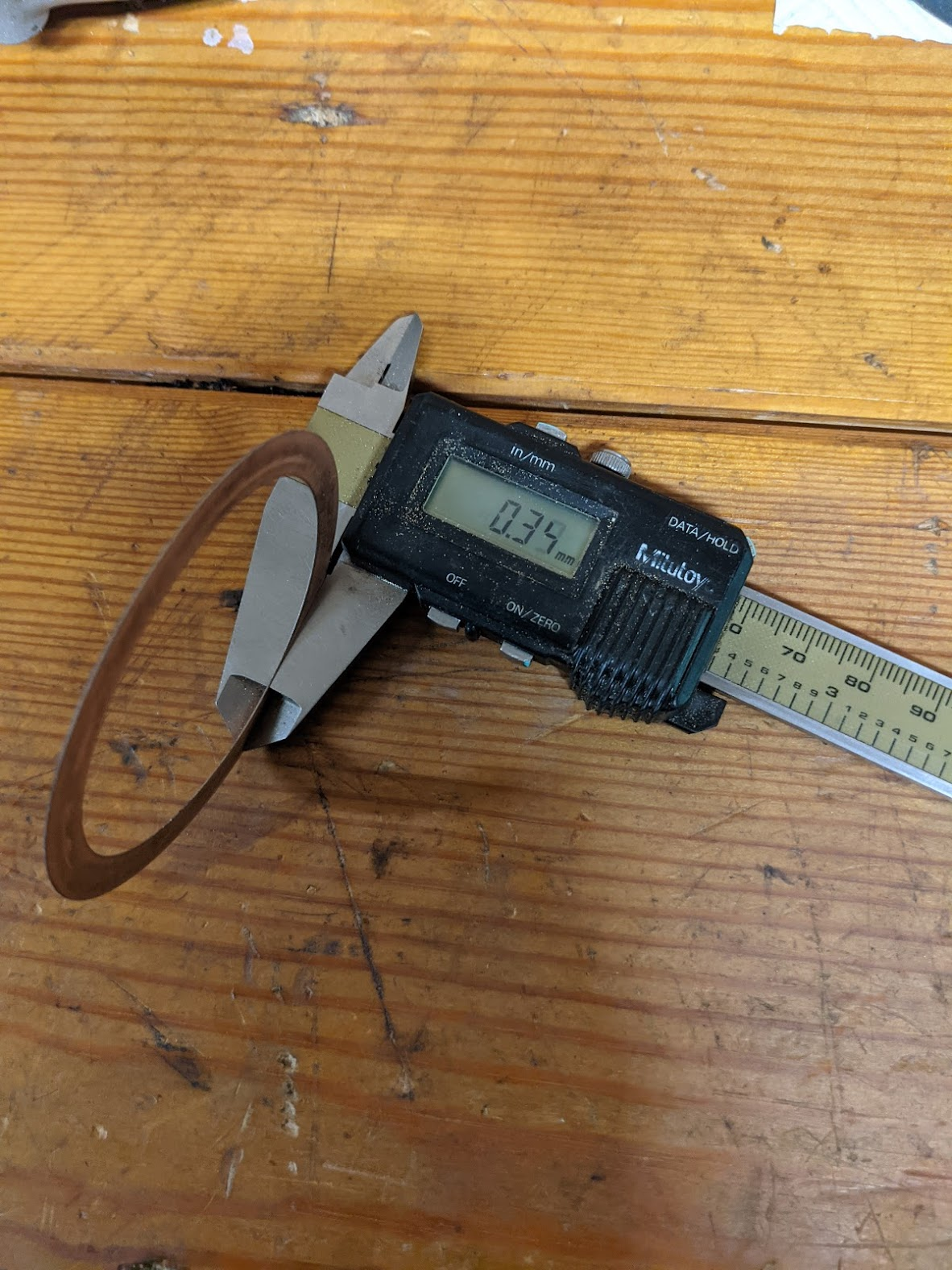
the genuine gasket (left) is 0.5mm and the aftermarket version (right) is about 30% thinner
Compression
The test for the piston and cylinder is a compression test:
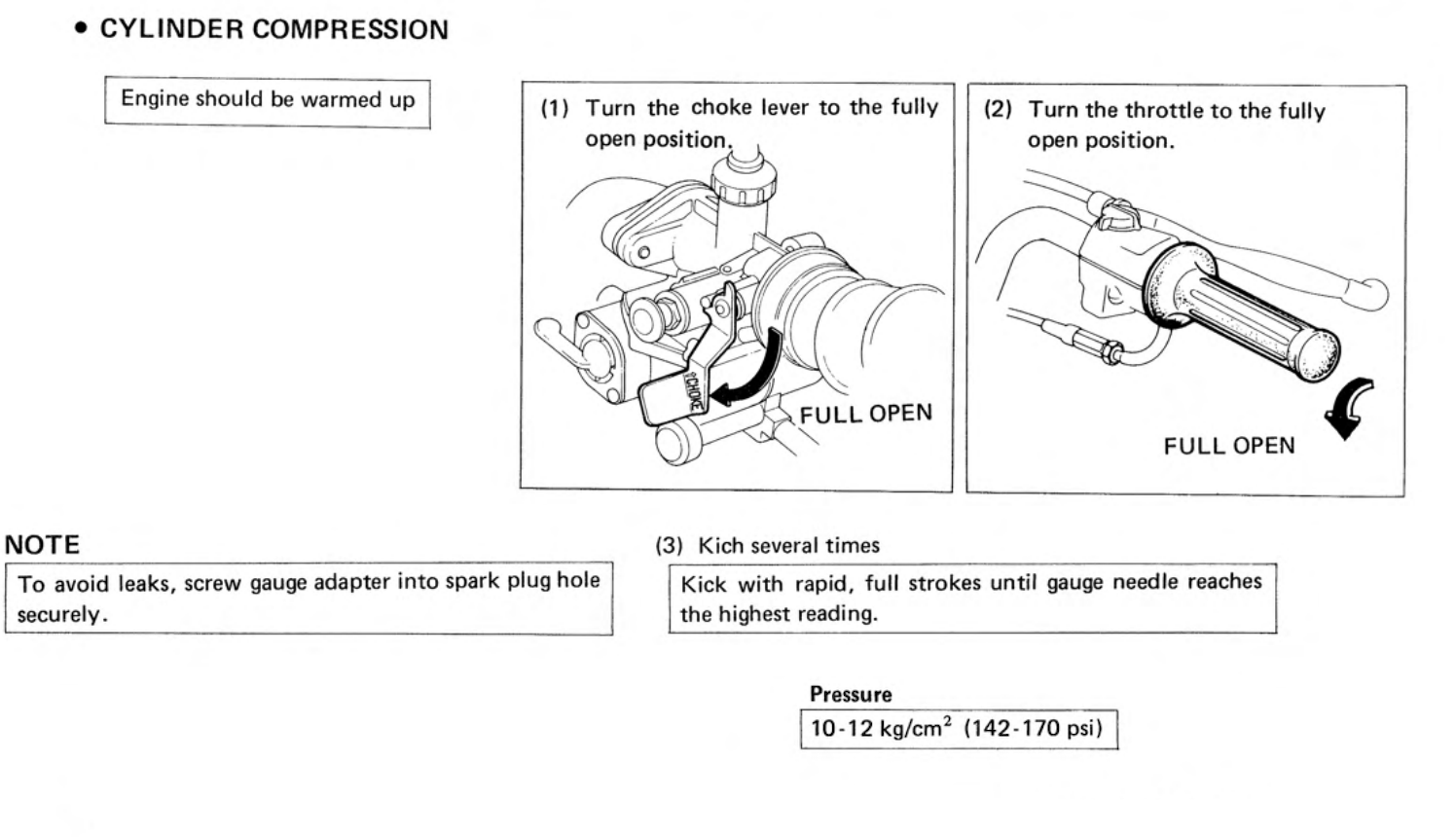
The normal value for a healthy 6v c90 engine is 170 psi and where compression is below 142 psi then the engine needs to be investigated for problems.
The possible causes of a pressure leak are shown below:
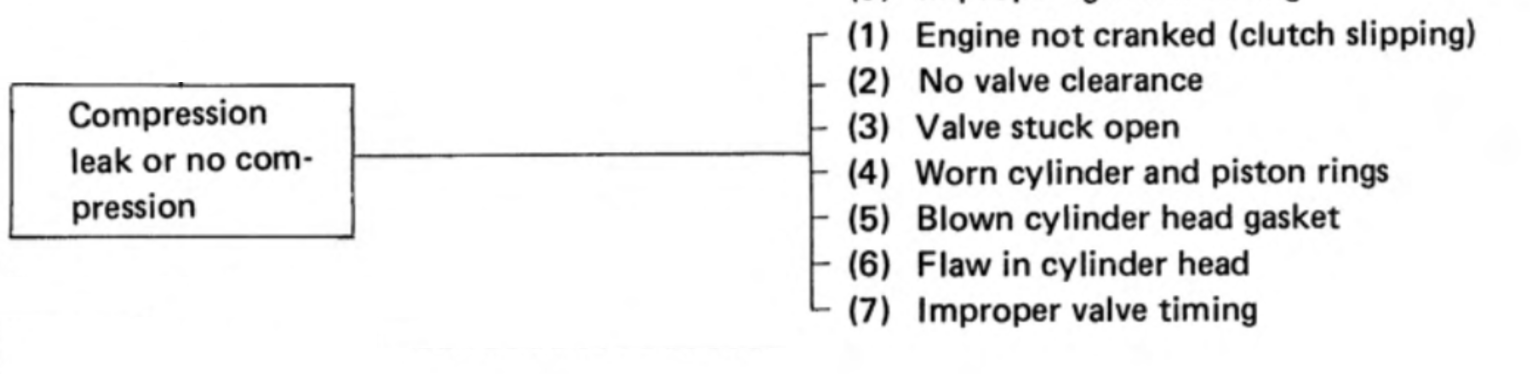
Where the engine is running normally and you are still getting low compression values you should check the test has been done properly (engine warm, choke and throttle fully open) and that your tester is working properly[5]. Per Honda's list above, the other possibility is that the engine is not cranking fully (for example because of poorly adjusted clutch).
Note that many of us will only have access to cheap compression tester sets and these can give misleading results. If you would like to know why - and how to fix it - I commend this excellent video:
https://www.youtube.com/watch?v=M0ZGGWx-rn8
References
1 | In addition to the explanation of engine knock by Kevin Cameron, this article by Allen W Cline provides an excellent overview: explaining the difference between knock and pre-ignition, the circumstances where they occur and the consequent problems they can cause.⏎ |
2 | The other major factor in engine knock is the quality of the fuel. The octane rating used by petrol(gasolene) producers is a measure of the fuel's ability to resist knock.⏎ |
3 | A Honda service bulletin from 1966 (SL#68) that says "oil reaches the joint from oil bearing chambers through internal porosity in the aluminium casting; such porosity is extremely difficult to avoid" indicating that perhaps the challenge was creating a non-porous casting.⏎ |
4 | Bentley commissioned the Corbin foundry - the foundry used by DFP - to make the pistons. Legend has it that Bentley was inspired by a novelty paperwait made from aluminum in the form of a piston that he saw on the desk of Doirot, one of the founders of DFP. ⏎ |
5 | it is sometimes said that using a tester with a long hose can effect results because the air that gets compresssed in the hose represents a relatively large volume compared to the small 89cc's being measured, although it is hard to tell if this is a signficant factor given that many of us amateurs are using very cheap testers of dubious quality. Note also the compression numbers are done at sea level - charts are available that outline the adjustments you should make if you are doing the measurements above sea level.⏎ |