what is a SIP? A SIP is a prefabricated panel consisting of two layers of Oriented Strand Board (OSB) sandwiching a layer of expanded polystyrene or urethane foam.
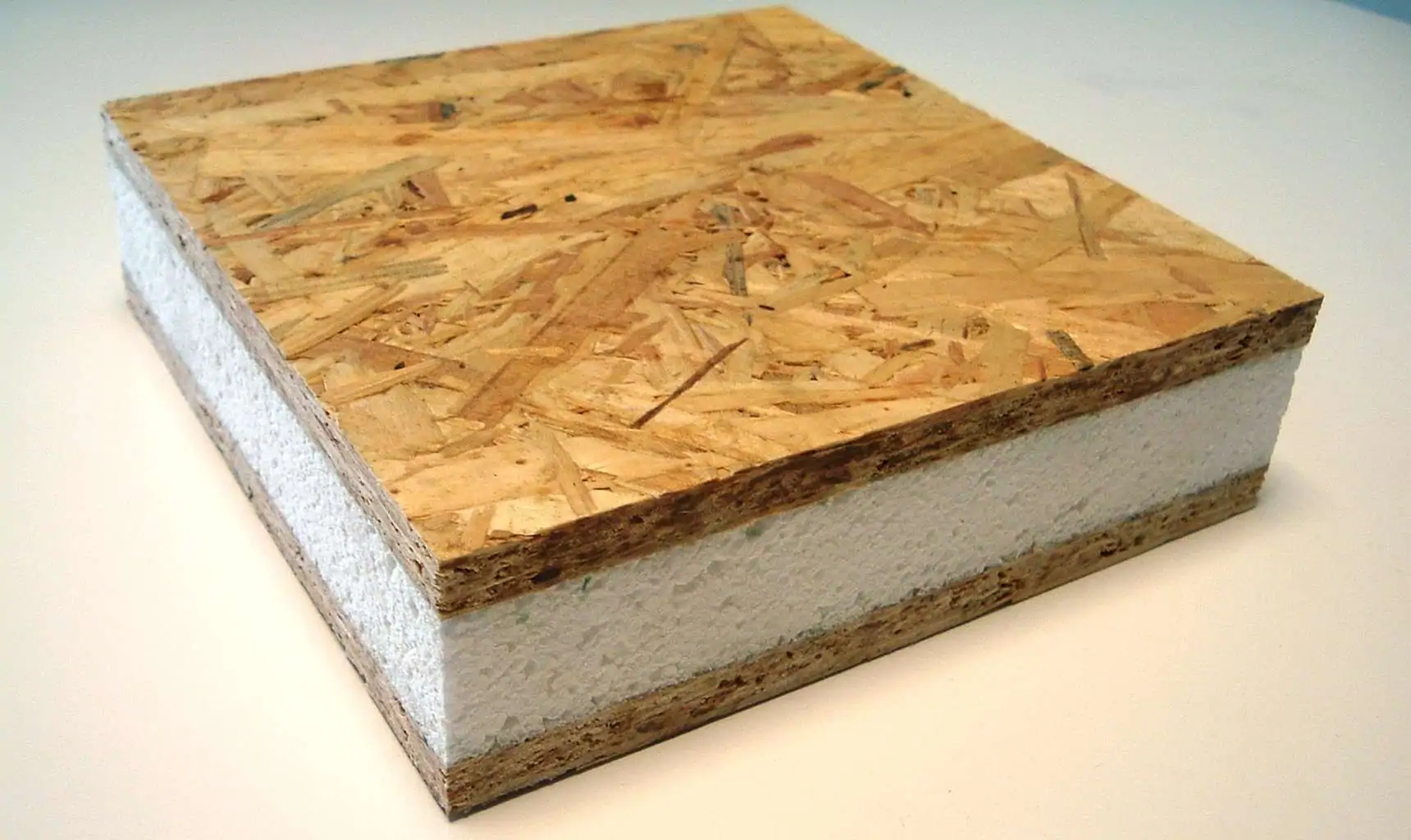
The history of building with SIPs
SIPs are a relative novelty in the UK – the majority of our houses are still built with brick and block – but the burgeoning interest in self-building and the desire to create energy efficient houses mean that SIPs are gaining in popularity.
This may surprise to our friends in the US where building with SIPs goes back to the 1950s. In fact the earliest laminated prefabricated panels (made from layers of plywood and tar paper) were used by Frank Lloyd Wright in the Usonian houses built in the 1930s:
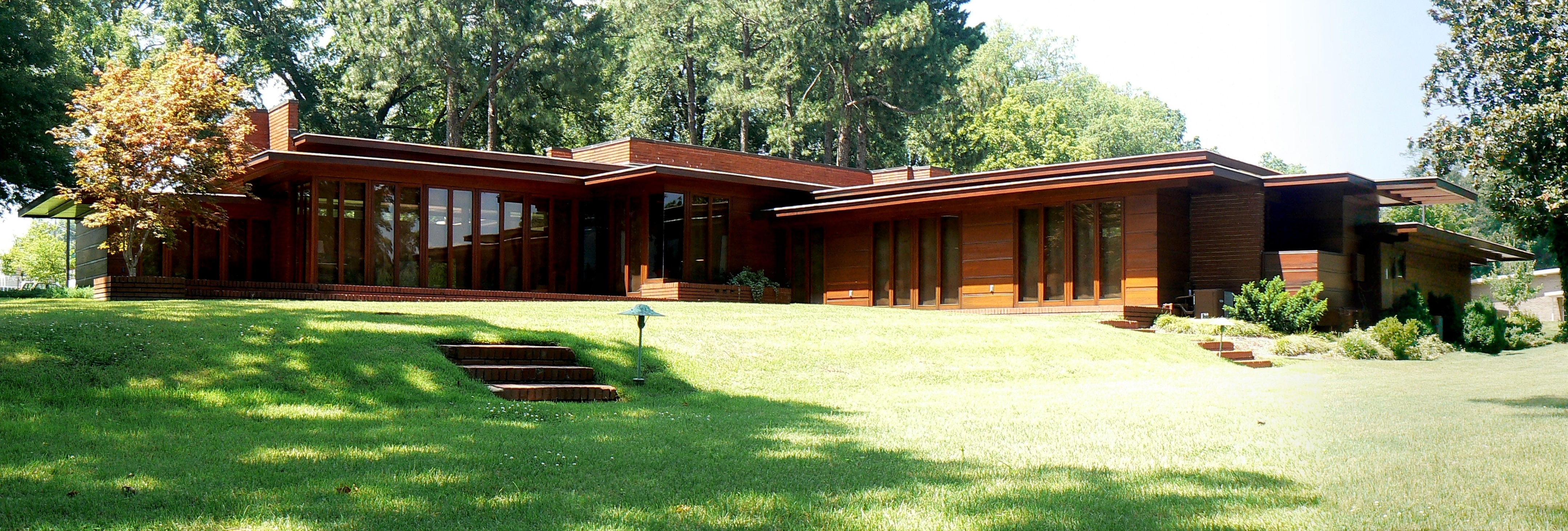
When reading about Frank Lloyd Wright’s laudable attempt to create affordable but beautiful homes I came across the English equivalent, Walter Segal.
Mr Segal (a naturalized Brit having escaped Nazi Germany) was also a pioneering architect who – inspired by the long tradition of simple timber framed buildings in the US – proposed a low cost, simple to construct design that he thought could help with the housing crisis that followed WW2.
The genius of his idea was that the designs were modular, configurable and designed to be put together by self-builders. His great belief was that there was a large part of the population who, if the process was made simple enough, could build themselves effective housing simply and cheaply.
He realised that by using readily available materials like standard plywood and plasterboard sheets, reducing the weight of the building – allowing our favourite plinth foundations – and removing the needs for wet trades like plastering, most competent DIYers could take care of the whole building process. And the icing on the cake was that, since the families who would live in the houses would also need to be involved in the design and build, this approach would create communities as well as houses.
An enterprising council in Lewisham sponsored the construction of about 50 of the houses in the 1980s. Walter died in 1985 but his ideas have continued to influence architects and self builders alike , and I hope in some small way are reflected in my shed. I am sure if he had lived another 20 years he would have been building with SIPs too.
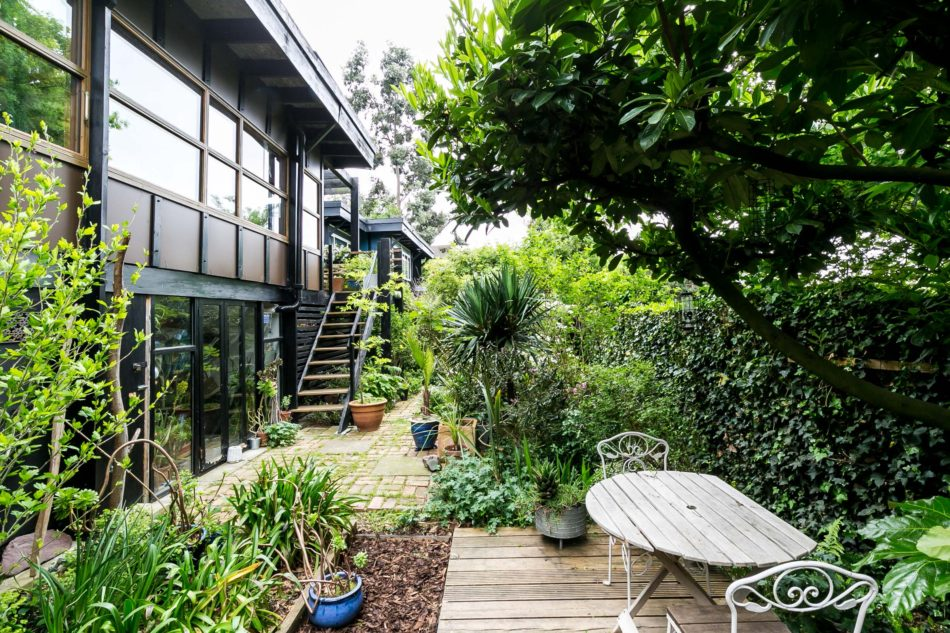
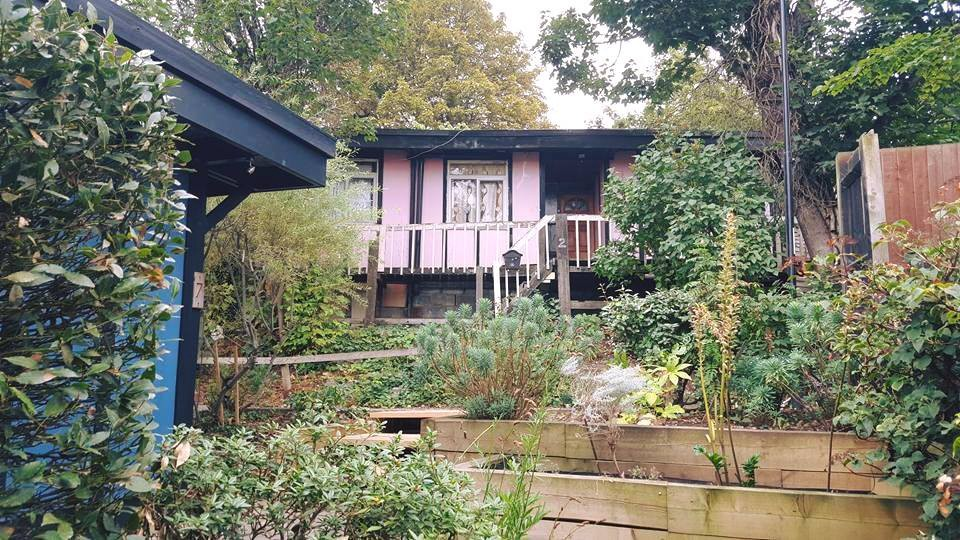
Read more about the brilliant Mr Segal here
Back to SIPs – Alden Dow (architect and brother of the founder of Dow Chemicals) was impressed by the Frank Lloyd Wright project, seeing how the panels could significantly reduce construction time, and saw an opportunity to improve the end result by adding insulation.
After much experimentation he developed a panel with an insulating core of styrofoam, thus inventing the first SIP. Although he built a number of houses using these panels it took several decades for a reasonably inexpensive production process to be worked out and, during that time, the cost of labour and the energy needed to heat even a poorly insulated house was still relatively cheap compared to material costs.
These factors hindered adoption of the ‘new’ technology, however today things are changing rapidly, and in the developed world labour and energy costs now represent a much bigger overall proportion of the costs of building, so we find ourselves at the dawn of the age of the SIP.
The advantages of SIPs
Despite being constructed from flimsy individual components SIPs are very strong. This is because when the two OSB boards are laminated together with the insulating foam core they act like narrow columns – the columns can take the load without twisting and buckling because they are glued in tension with the core.
The boards can be joined together in a few ways but in each case a rebate is made in the foam and this can receive either a pair of thin OSB splines, a mini-SIPs or a piece of timber. These joining components are glued and nailed to the panels adding further strength. For SIP floors and roofs the timbers act as inbuilt joists/rafters allowing the panels to span surprising distances without further support.
When the boards are glued and nailed, the glue helps to improve air tightness, and this in turn helps improve thermal efficiency.
Since the panels go together in big pieces and with basic tools like a nail and glue gun structures can be erected very quickly.
Finally, the panels can be cut and prefabricated to your design by the supplier, further reducing your build time (if you have access to a crane!).
So there you have it, structurally sound, thermally efficient and quick to build with – it really is crazy that they are not used more often.
How strong are they? It is possible to build 4 story buildings exclusively with SIPs (no secondary supports) – For example the very cool example in Wyoming
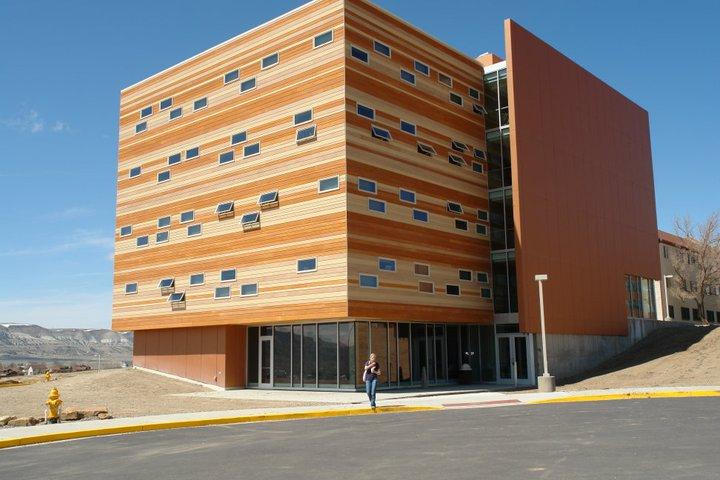
Anyhow, they are definitely strong, and here is a picture of one with an elephant standing on it to prove it
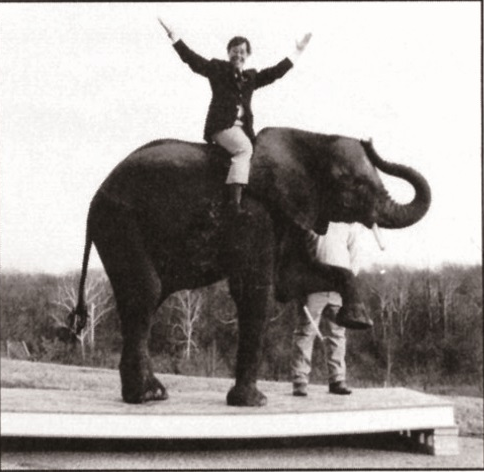