The crucible steel made in Sheffield maintained a reputation as the best steel in the world for nearly two centuries. This success was built on a combination of skill, quality raw materials and the commercial brilliance of the UK’s manufacturing heartlands of the 18th and 19th centuries.
The principle ingredient of Crucible steel was Swedish blister-steel. This material was far from perfect though, since the process used to create it meant that carbon was not absorbed consistently throughout the metal. Because the amount of carbon in the metal determines how it hardens when heat-treated, this was problematic for a number of industries and particularly for edge tool manufacturers who needed to create tools with a consistently hard edge.
During the 1740s Benjamin Huntsman invented a technique that resolved this shortcoming and, although simple in principle (he melted the blister steel bars and then poured them into an ingot), Huntsman had to first design a furnace that was capable of melting the blister steel and this required reaching temperatures far in excess of the capabilities of the furnaces available at the time.
Although Huntsman’s initial aspirations were modest – he was a watchmaker and wanted to improve the quality of the steel used in his clock springs – his invention soon found other applications and was to become one of the more important discoveries in the history of modern industry, paving the way for the work of Bessemer and Siemens who invented the bulk steel production processes that changed the industrialised world forever.
The steel made using Huntsman’s technology was known simply as ‘cast steel’ for over a 100 years, but after the same term was adopted to describe the inferior steel made by the technique Bessemer invented towards the end of the 19th C the term ‘crucible steel’ was adopted to distinguish the steel made from the older process.
Crucible Steel Furnaces
Huntsman’s furnace design remained largely unchanged for over 200 years, right up until the end of crucible steel production in the middle of the 20th century:
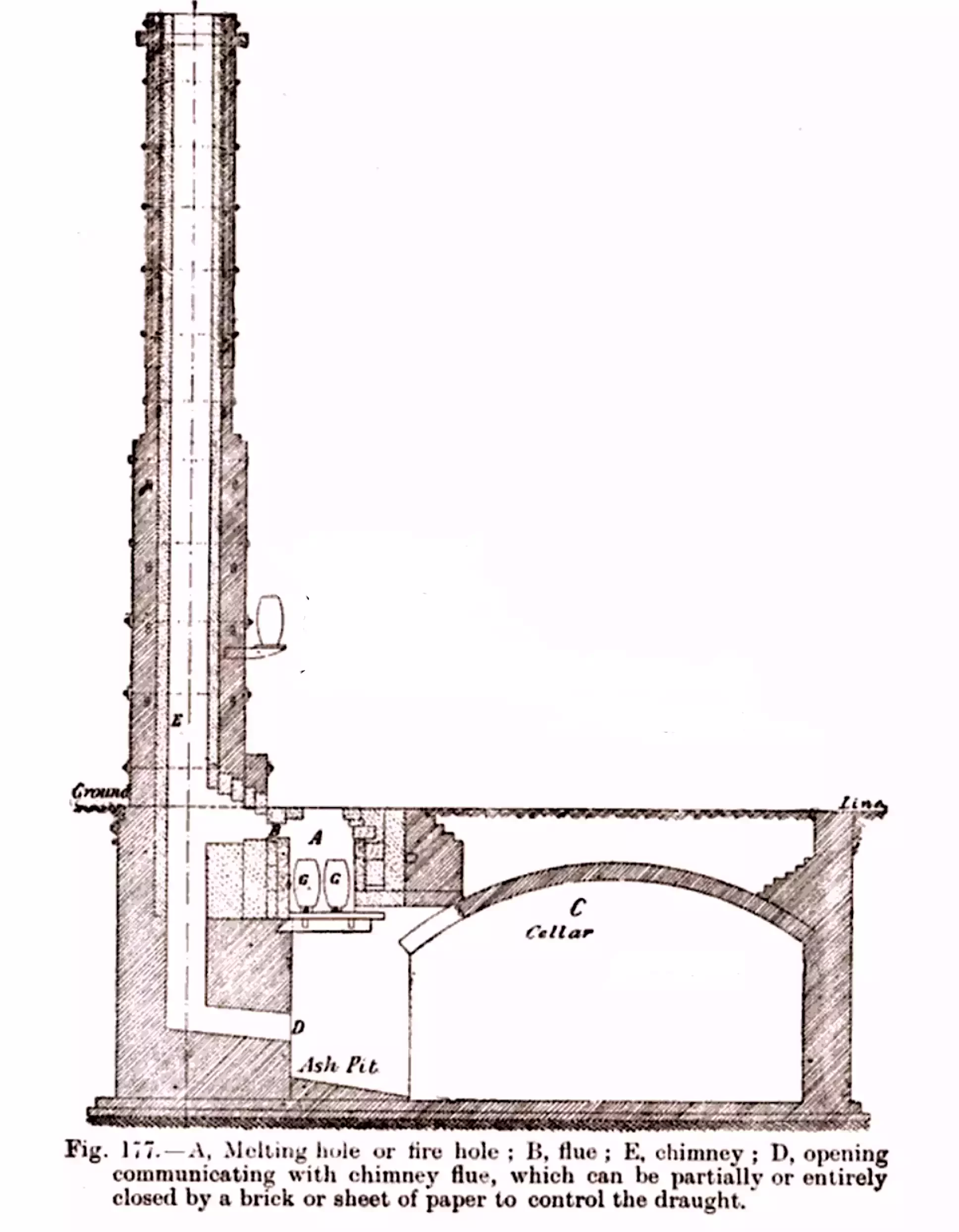
The melting holes (A) were about 2 ft square and 3 ft deep and the top of the furnace is at the level of the floor. The top of each melting hole is covered with a hinged lid of firebrick in an iron frame with a handle, beneath which the melting pots (G) were sat on a grate, with an ash pit (D) underneath that can be accessed via an arched cellar (C).
Each melting hole is connected by a flue (B) to a chimney stack (E) that serves 5 or 6 furnaces arranged in a line on the side of the casting house, leaving the floor clear for casting operations.
The arrangement of the chimneys resulted in the distinctive architectural style shown in the cut-away drawing below. The melting holes are at the base of the chimney stack, and the underground cellar entrances can be seen below the floor:
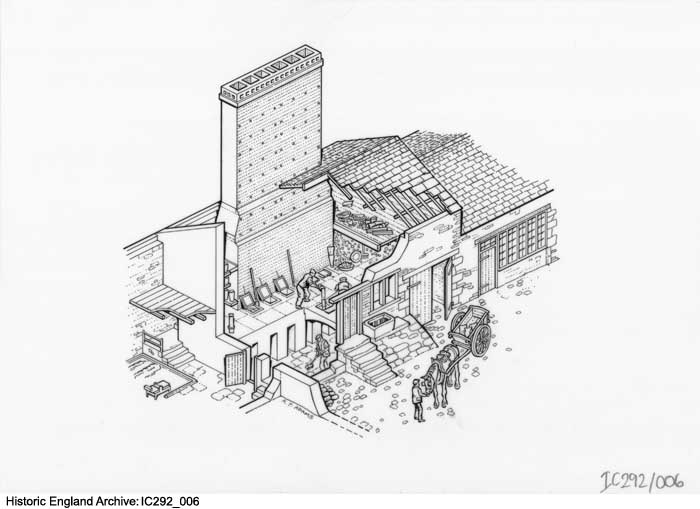
Crucible Manufacture
Making crucible steel was an expensive business, starting with the clay pots (“crucibles”) which were needed in large quantities and – because they were very delicate -were typically made on site at the steel works.
The pots were made from special mixes of clays selected to be able to withstand the extremely high temperature of the furnaces – the exact recipes for which were prized trade secrets – and were traditionally mixed by treading and kneading with bare feet.
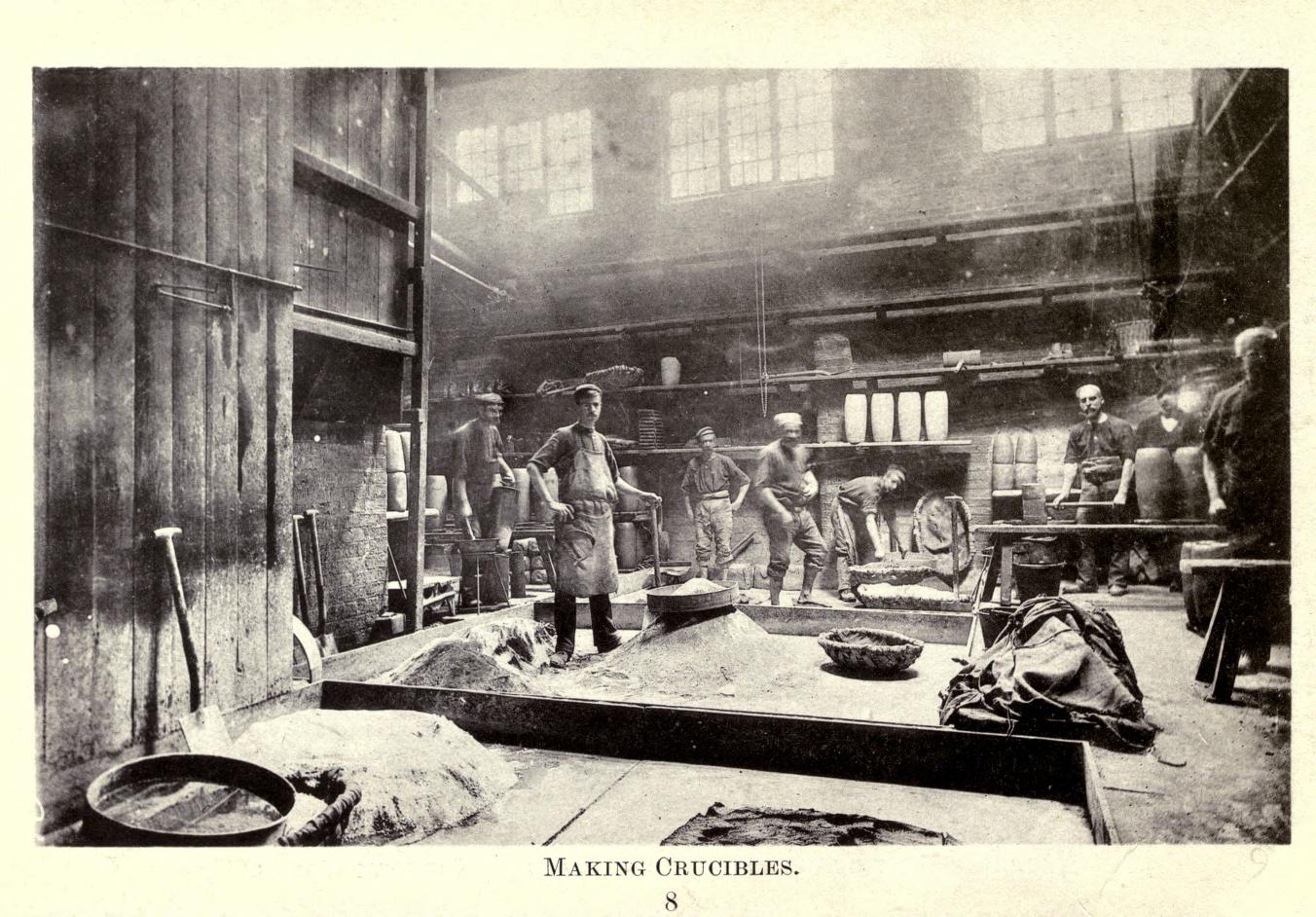
The pots were dried for two or three days on a shelf in the pot house and then moved to the melting shop on to a shelf above the melting holes where they dried for a long period, sometimes up to 6 weeks.
The crucibles were only good for three melts before they had to be replaced. Common practice was to run two shifts per day (one in the daytime, the other over night) and to perform three melts per shift, so even a small furnace with say 6 or 12 melting holes needed dozens of new pots each week. To give some idea of the scale of the efforts devoted to making crucibles in Sheffield, R Hadfield, writing for the Journal of The Iron and Steel trade in 1894 said “Sheffield now uses weekly some 14,000 clay crucibles in which fuses its steel”.
Each pot was between 15-20 inches high and 9 inches at the widest part and, when new, could be charged with between 50 and 60 lbs of metal. The size of the charge was reduced in the 2nd and 3rd melts since the slag that gathered on the surface of the molten metal corroded the tops of the pots meaning they had to be loaded with smaller charges at each subsequent melt.
Melting
The crucibles – having been previously annealed to a red heat overnight – were filled with broken blister steel bar (blister steel being the preferred choice for making the best grades of tool steel), covered with a lid and a pair of them placed in each melting hole which was then filled with coke and burned for around an hour, after which another charge of coke was added and burned and then the lid was removed to make sure that the metal was molten and – if not – the furnace was charged with coke for a third time.
The puller-out, as the name suggests, was responsible for extracting the crucible from the furnace once the head melter was satisfied that the pot was ready for ‘teeming’ (pouring).
For the finest grades of steel the metal was not poured immediately on melting, but was held in the furnace for a period of time in a process called ‘killing’ . The extended heating counteracted the tendency of the metal to form blow holes that showed as a sponge-like bubbles in the final ingot. The timing of this step – critical for a quality product – was entirely dependent on the skill and experience of the head melter. The experience of the workers managing the process were paramount – even subtle differences in the process could impact the quality of the metal, for instance in this account it was said that only common grade steel was made on a Monday since at that point the furnace was not at full temperature meaning the proper length for killing could not be reliably judged The Metallurgy of Steel, Volume 1.
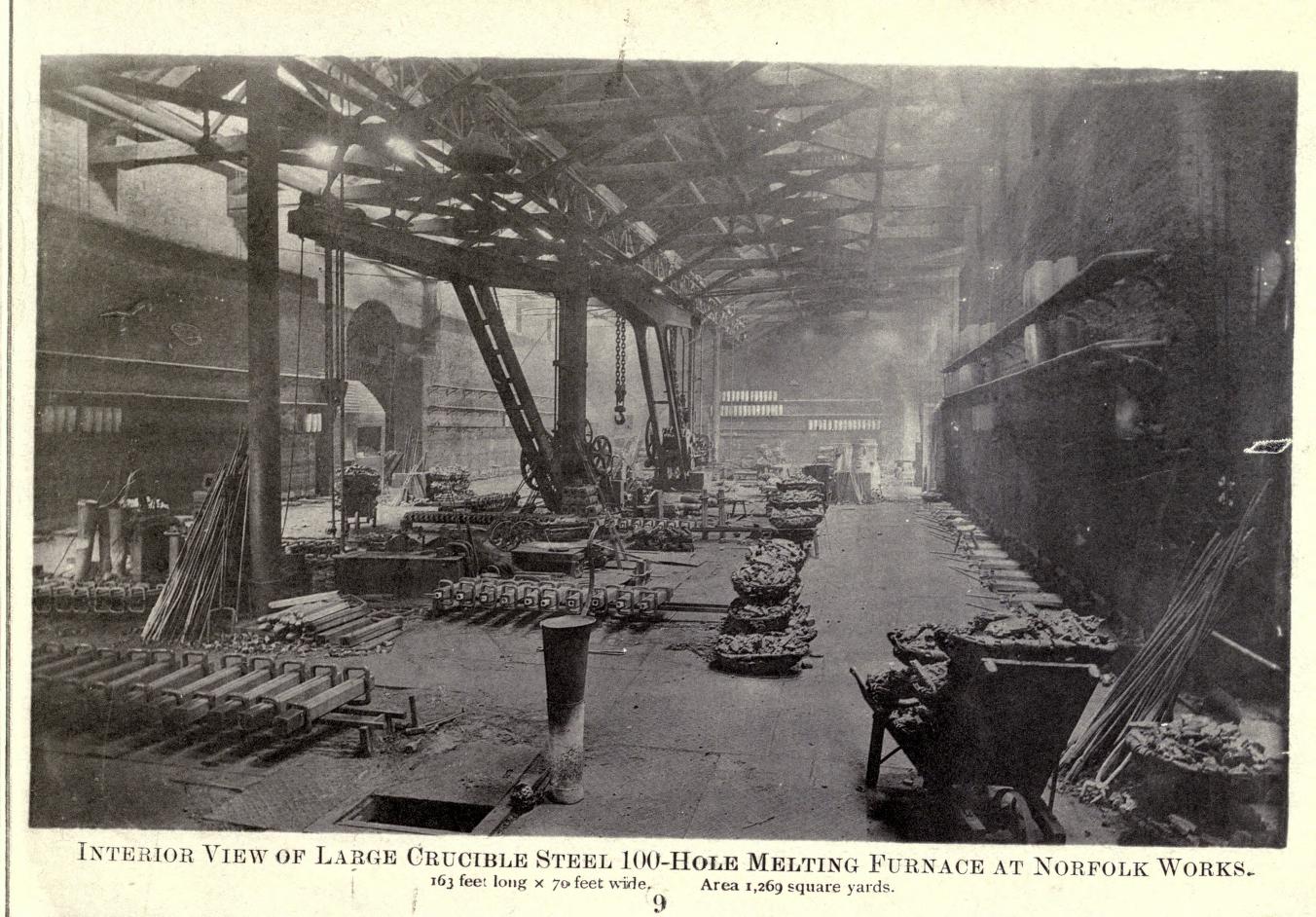
Teeming
When instructed by the melter, the puller out – whose arms and legs were wrapped with wet sacking to protect him from the extreme temperature of the furnace – lifts the crucible with a pair of long tongs and in a single motion places it on the melting house floor where it is cleaned of coke and slag on the outside, the lid taken of, the slag skimmed of using a “mop” (a thin bar with a knob of slag already attached to the end). Next, the pot is transferred to the teeming hole where the teemer pours it into a cast-iron mould. The mould is constructed in two pieces held together with rings and wedges and set at a slanting position in recesses – known as teeming holes – in the floor[1].
Teeming was a highly skilled and physically demanding job requiring the metal to be poured in a single continuous motion, making sure that it does not touch the side of the mould (not as easy as it sounds, since the moulds were typically around 3in square and 30 inches long). If poured badly, say because the flow was interrupted or the metal touched he side of the mould and solidified then the ingot would be imperfect. According to an account from 1901 the weight of the crucible and steel contained was about 70 lbs and the teemer was required to lift and poor about 10-15 cwt (80-120 stones) of steel in the space of about 20 minutes[2]
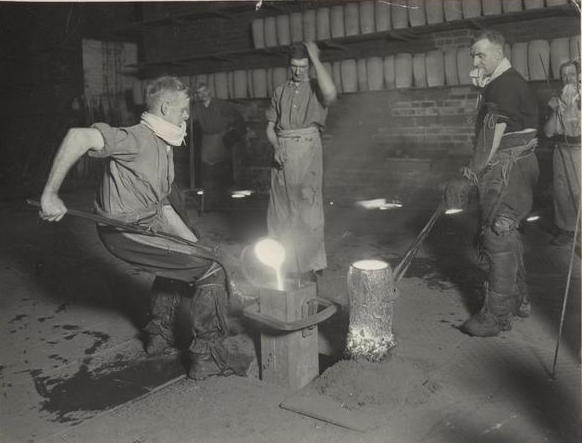
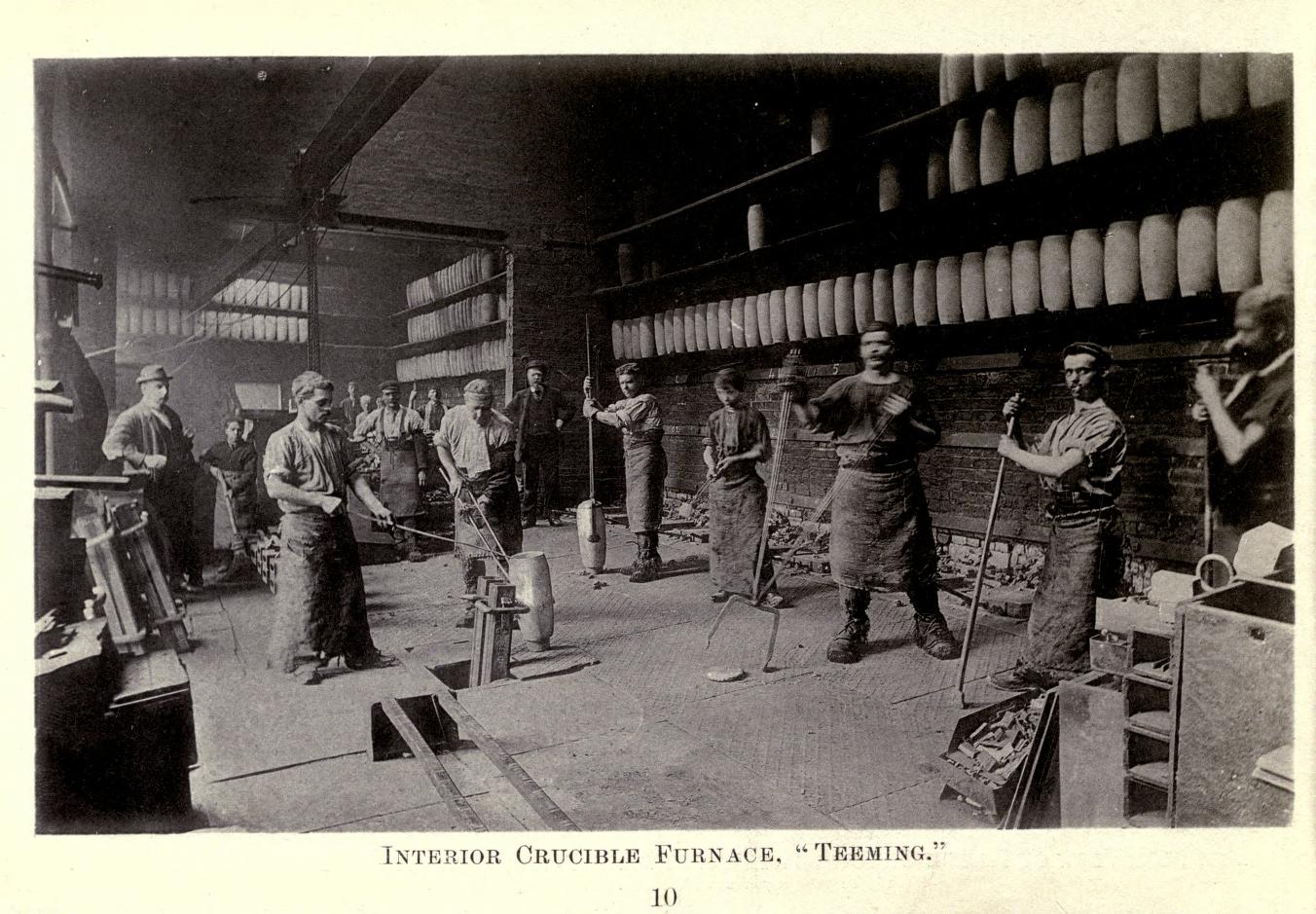
Immediately after teeming the pots are taken back to the melting hole, where they are made ready for another charge. The first heat takes 4-6 hours, the second and third take 2-3, at which point the crucible is spent.
The timing required for melting, killing and teeming required sound judgement and skill – too early or too late and the ingot is no good – and it was also critical that no coke got into the metal else the impurities could make the resulting ingot liable to break when heated and forged (a property known as being ‘hot short’ in the trade).
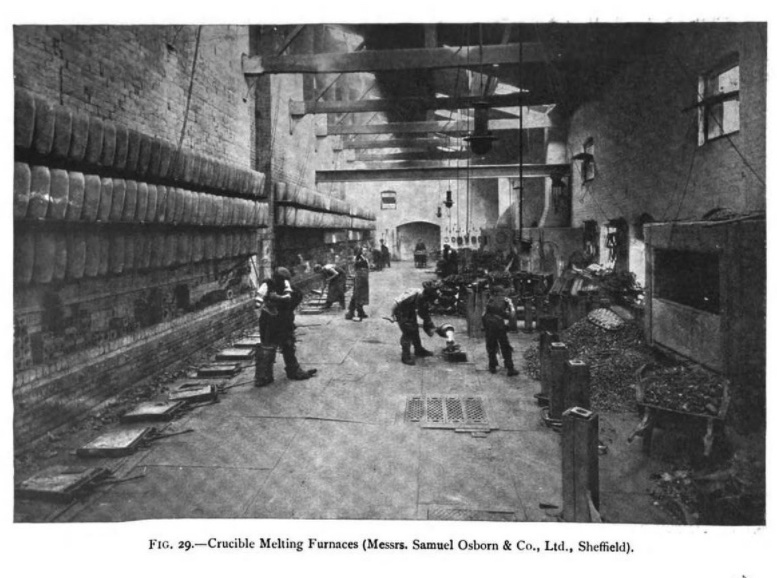
Topping
In the final step the ingot is topped, that is to say, once cold the end is broken off so the melter can judge the condition of the metal according to how it fractures. It was said that experienced melters could judge the quantity of carbon (temper) of crucible steel to within one tenth percent of the actual value this way3
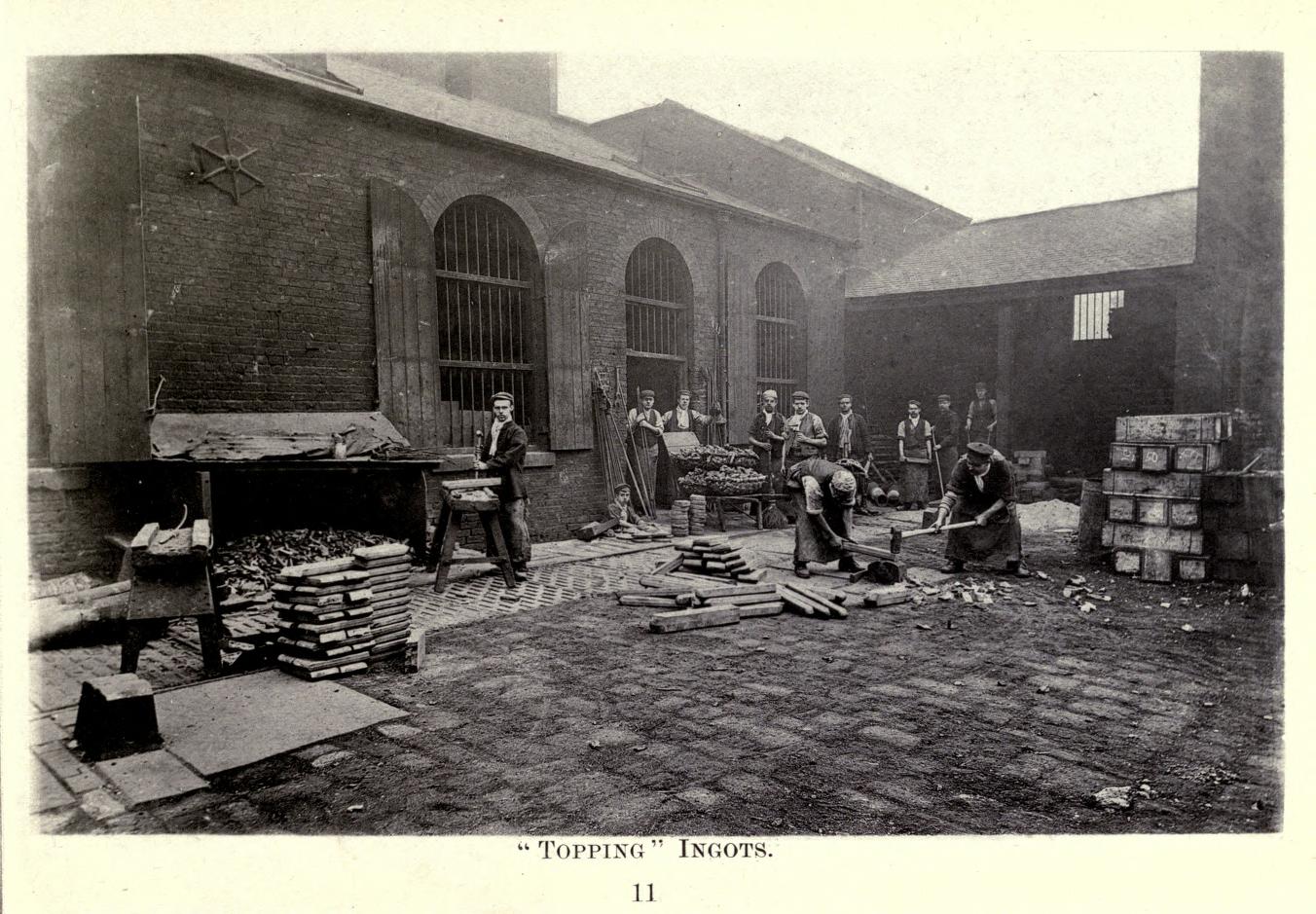
Grade and Temper
Crucible steel was sold according to its grade, ie the quality of steel, which is determined by the raw materials and method of melting employed (the best quality steels were ‘killed’ as described above) and its temper, which refers to the quantity of carbon, which determines the metal’s hardness and toughness when heat treated, and thus its intended application.
Although the finest tool steel was made using selected tempers of blister steel made from Swedish bar iron, there were other methods for making crucible steel. For instance common (cheaper) grades were made by taking low-carbon bar iron and increasing the carbon content with charcoal; or by taking high-carbon pig iron and diluting the carbon content with added bar-iron. Some of the ‘recipes’ are described below:
I. Select cut bar iron and ‘fetch it up’ by the addition of charcoal. Melt and teem.
II. Use broken pig iron and ‘let it down’ to the required temper with cut bar iron. Melt and teem.
III. Select blister steel of the desired percentage carbon. Melt, kill and teem
IV. select blister steel which is a little too hard and ‘let it down’ with a smaller quantity of milder steel scrap.Melt, kill and teem.
IV. select blister steel which is a little too hard and ‘let it down’ with a smaller quantity of milder steel scrap.Melt, kill and teem.
The principles and practice of iron and steel manufacture, Walter Macfarlane, 1921 (1906)
Steel makers were thus able to offer many grades of crucible steel to suit their customers purses and needs. The classifications varied from the admirably simple, for example William Jessops and Sons offered 3 grades: yellow label (warranted/best), green label (second grade) and black label (third grade); to the bizarrely convoluted, for instance Firth’s effort from 1913:
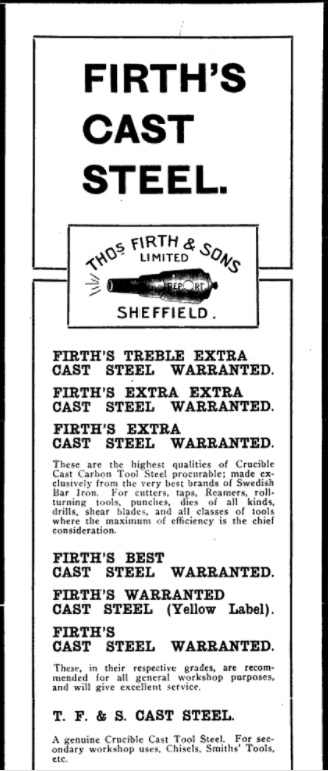
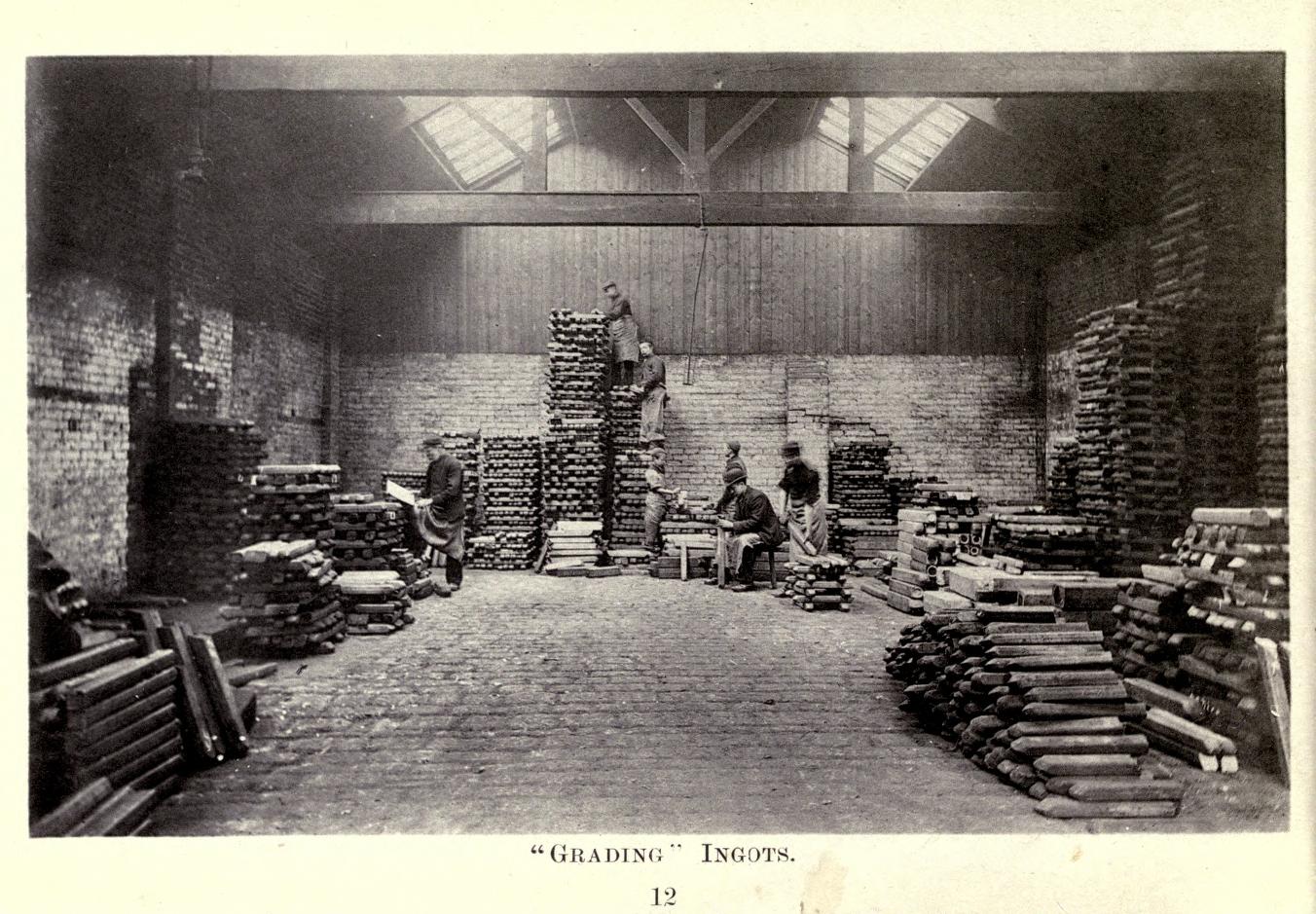
Manpower
The exact staffing arrangements differed from factory to factory, but a 12 hole furnace typically needed about 7 men to run it, including a head melter, 2 pullers out and a some combination of teemers, cellar boys, odd-men, and yardmen[4]
The role of the melter, puller out and teemers are described above. The yardman wheeled coke from the coke bins to the furnace; the odd-man assisted generally and attended to the crucible annealing furnace, and the cellar lad was employed making crucible lids and stands and checking the crucibles for cracks from the cellar below during the melts.
When you consider that at the end of the 19th C Sheffield was producing more than 1000 tons of the best quality crucible steel per week (and many times that volume of other grades[5] and that a 12-hole furnace could only produce 25 tons of tool steel per week – a feat that required it to run continuously for 6 day shifts and 5 night shifts, each of which would have to do 3 melts[6] you can begin to appreciate the scale and cost of the crucible steel operations in Sheffield. Add in the capital and maintenance costs for the furnace, cost of fuel (each ton of steel consumed 3 tons of coke), the cost of crucible manufacture and the expensive raw materials needed for the best steel and the result was that crucible steel was a very expensive product[7]
It is a testament to the enduring reputation for crucible steel that it continued to be made over such a long period despite the limited opportunities to make the production processes more efficient and the availability of much cheaper alternatives. Of course, despite its well deserved reputation, it was inevitable that the inefficient and hard-to-scale process would eventually become obsolete, and that is what we will cover in the next post.
References
1⏎ | The Chemical News and Journal of Physical Science, 1870 |
2⏎ | D. Flather, ‘Crucible Steel; Its Manufacture and Treatment‘, The Staffordshire Iron and Steel Institute (1901-02), p62, David Flather was a famous Sheffield metallurgist and tool maker |
3⏎ | D Flather, op-cit |
4⏎ | c.f The Metallurgy of Steel by Mr Henry M Howe, 1887 , Liquid steel: its manufacture and cost, By David Carnegie, 1913 |
5⏎ | R Hadfield, writing for the Journal of The Iron and Steel trade |
6⏎ | Liquid Steel p77 |
7⏎ | as a comparison Steel created via the Bessemer process was less that 1/5th of the price: see Liquid Steel |