Finished off the walls by fixing the structural posts and beams in the near corner (these will frame the window and door).
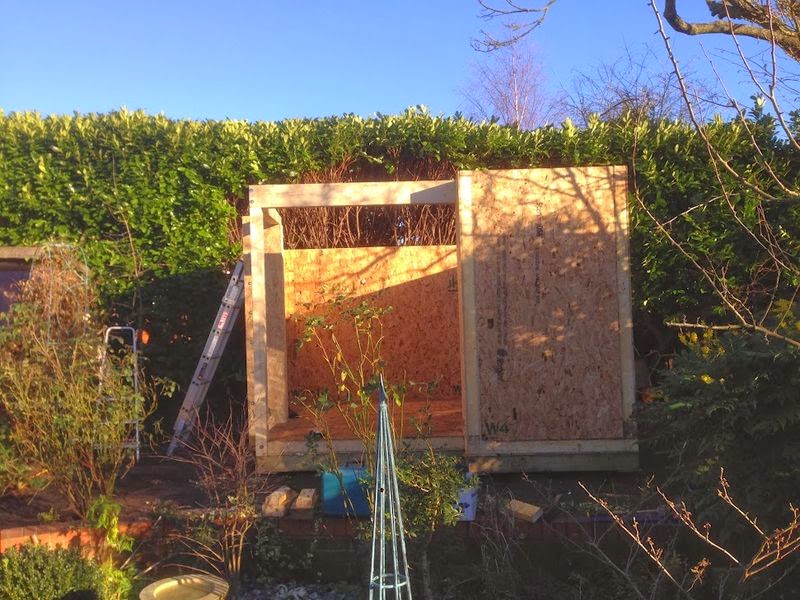
A post is needed to support one corner of the roof. When I did the drawings I arranged it so that the post sat directly on the sub-frame inside a cut out in the floor panel, thinking I could then insert a single coach screw through each side of the post into the facing timbers on the SIP floor. When I came to do this it occurred to me that this might be a little flimsy given that the post will have to take the brunt of the sliding door being opened and closed.
Anyhow, I could not think of a better way so left it as is – hopefully the weight of the roof will stop it from wiggling around. Talking of which, the weight of the roof turned out to be the biggest problem we had putting everything together.
raising the roof
The roof is made of 150mm SIP panels that are 1.2m x 4m. Although me and Dave could lift them it was obvious that we were never going to be able to get them on top of the walls – they were far too heavy.
This was a dilemma – I had the offer of help from two strapping neighbours on Sunday, however the weather forecast from the evening onwards was dire and we had just effectively created a giant impossible-to-waterproof OSB bucket that would surely be turned to paper-mache by the ensuing downpours.
I also had serious concerns about our managing even with 4 of us – the main issue was there was not enough room to manoeuvre the a panels through the door opening and onto the (low) rear wall from inside the building. This meant we would have to push them from ground level over the front wall – a good 2.5M up – and that most of the shoving would have to happen well above head height. The panels are about 180kg each and without any kind of suitable platform or lifting gear this seemed rather perilous.
So, drastic action was needed – SIP fans of a sensitive disposition should look away now – and I decided to cut the panels in half along the longest length. This meant we could push them through the door opening and swing them on to the walls with (relative) ease.
The panels were simple to cut laterally using a chop saw to go through OSB facings. After the facings were cut the panels were kept intact by the foam core, but when pushed over onto a piece of raised timber along the length of the cut this snapped cleanly along the break in a rather pleasing manner.
What are the consequences of this butchery? Well obviously I will have degraded the strength of the roof and, although I am able to walk around on it without noticing any flex, I obviously won’t be starting a tap dancing school up there.
I glued the panels back together when on the roof, so I think impact on heat retention will be minimal – it should also still be wind-tight after I fit the roof membrane.
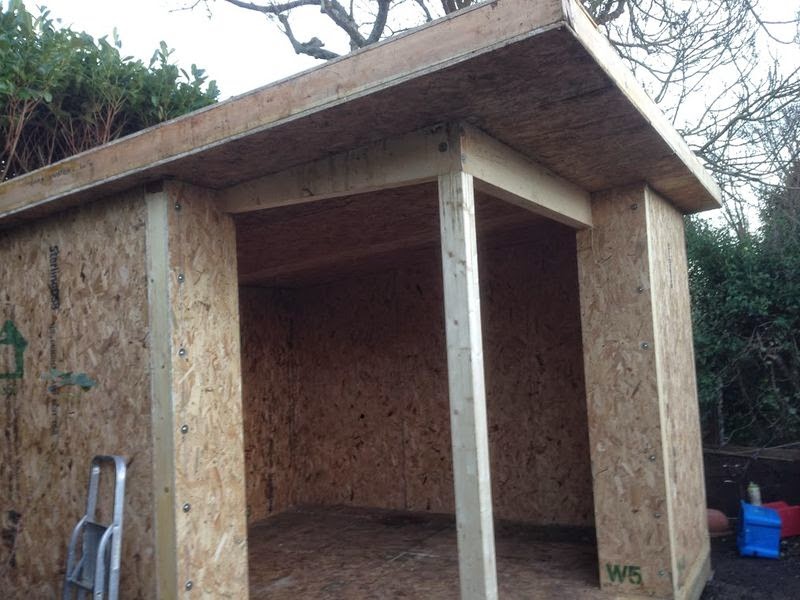
lessons learned
clear off any excess glue that squeezes out of the joints *before* it goes off. It is a lot easier than doing it later.
Hire one of these:
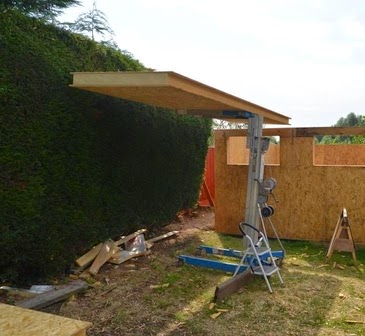